Composite materials are revolutionizing various industries, from aerospace to sporting goods. The innovative properties of composites are making them a preferred choice for many applications, including their high strength-to-weight ratio, durability, and flexibility. In this article, we will explore the latest innovations in composite materials and how they are being used in different sectors.
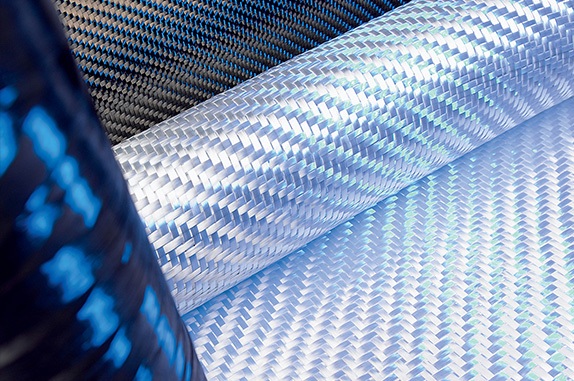
What are composite materials?
It is a combination of two or more materials that have different physical and chemical properties. They are engineered to achieve specific performance properties, such as strength, durability, and flexibility. Composites consist of a matrix material that holds the reinforcement fibres or particles in place.
Types of composite materials
There are three main types of composite materials:
Polymer matrix composites (PMCs)
Polymer matrix composites (PMCs) are materials composed of a polymer resin matrix, such as epoxy or polyester, reinforced with fibres or particles, such as carbon, glass, or ceramic. These materials offer high strength-to-weight ratios, stiffness, and durability, making them useful for a variety of applications in aerospace, automotive, marine, and sporting goods industries, among others. PMCs are commonly used for structural components, such as aircraft wings, helicopter blades, and racing car bodies. They can also be used for non-structural components, such as electrical insulation, thermal protection, and corrosion resistance.
The properties of PMCs can be tailored by choosing the type, orientation, and volume fraction of the reinforcement, as well as the type and amount of the polymer matrix. However, PMCs are susceptible to damage from impacts, scratches, and moisture, which can reduce their mechanical properties over time.
Metal matrix composites (MMCs)
Metal matrix composites (MMCs) are materials consisting of a metal matrix, such as aluminium, magnesium, or titanium, reinforced with a secondary phase, such as ceramic, metallic, or carbon fibres. The combination of the metal matrix and the reinforcement provides enhanced properties, such as improved strength, stiffness, wear resistance, and thermal conductivity.
MMCs are commonly used in aerospace, automotive, and electronic industries due to their high performance and lightweight properties. They can be manufactured using various methods, such as powder metallurgy, casting, and infiltration. The properties of MMCs can be tailored by adjusting the type, orientation, and volume fraction of the reinforcement, as well as the type and amount of the metal matrix. However, MMCs can be more difficult to manufacture and more expensive compared to conventional metals.
Ceramic matrix composites (CMCs)
Ceramic matrix composites (CMCs) are materials composed of a ceramic matrix, such as silicon carbide, alumina, or zirconia, reinforced with fibres or particles, such as carbon, silicon carbide, or alumina. CMCs offer high strength, stiffness, wear resistance, and thermal stability, making them suitable for high-temperature applications in aerospace, energy, and industrial sectors.
CMCs can withstand temperatures up to 2000°C, which is higher than most metals and polymers. They can be manufactured using various methods, such as chemical vapor infiltration, liquid infiltration, and melt infiltration. The properties of CMCs can be tailored by adjusting the type, orientation, and volume fraction of the reinforcement, as well as the type and amount of the ceramic matrix. However, CMCs can be brittle and more susceptible to damage from impacts compared to other composites.
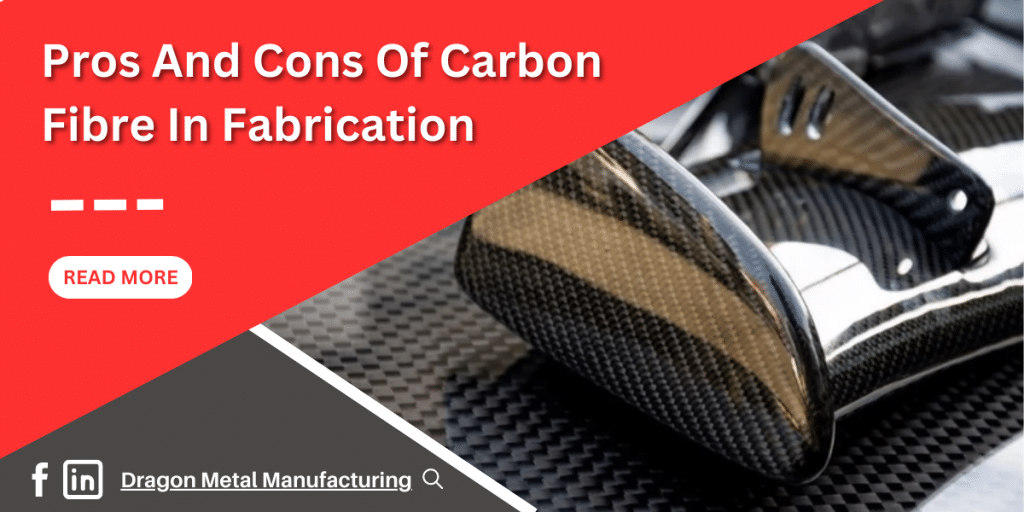
Different Processes of Manufacturing Composite Material
Wet Lay-up
Wet lay-up is a simple and flexible manufacturing process for composite materials that is widely used in the marine industry. The process involves building up the component in a mould by applying several layers of reinforcement and wet resin, which is distributed using a roller until the desired thickness is achieved. The resin is then cured, with the option of using applied heat, if necessary, to produce the finished component.
In this process, a dry fabric of the reinforcing material is laid out on a mould, which is then impregnated with resin using a brush, roller, or sprayer. Excess resin is squeezed out using a squeegee or roller. Wet lay-up is particularly useful for producing large, flat, and low-stress composite structures. Although material costs are relatively low, the process is labour intensive and suffers from high styrene emissions. Nonetheless, wet lay-up remains a popular choice due to its affordability and flexibility.
Spray-up
Spray-up is a manufacturing process for composite materials that uses a spray gun to apply chopped fibre reinforcement and wet resin to a mould, building up the desired thickness of material. This process is faster and cheaper than wet lay-up, but the mechanical properties are generally lower. Spray-up is commonly used for large and relatively simple structures like bathtubs, boat hulls, and storage tanks.
Like wet lay-up, spray-up involves impregnating a dry fabric with resin to produce the composite material. However, with spray-up, resin and chopped fibres are applied simultaneously onto the mould, allowing for faster production times. The resulting composite is cured under controlled conditions. Spray-up is ideal for producing large, curved, and low-stress composite structures.
Compression Moulding
Compression moulding is a widely used manufacturing process for composite materials that involves placing dry fibres or pre-impregnated fabrics in a heated mould. Once closed, pressure is applied to compress the fibres and cure the resin, producing high-strength and low-weight composite structures with intricate shapes. The process is particularly suitable for generating a Class A surface finish, and its similarity to the stamping process used for sheet metals has led to applications in the automotive industry.
A charge of fibre and resin, either sheet moulding compound or bulk moulding compound, is used in the compression moulding process. The charge is placed in a preheated mould, which is then closed and held under pressure until the resin is cured. While the process requires high investment in heated tooling, it is still suitable for medium to high volume production. Compression moulding is an ideal choice for generating high-strength, low-weight composite structures with intricate shapes that require a Class A surface finish, and is increasingly being used in the automotive industry.
Injection Moulding
Injection moulding is a versatile process used primarily in the plastics industry, but it can also be used to manufacture composite materials. This process involves placing dry fibres or pre-impregnated fabrics in a heated mould, which is then closed. Resin is then injected into the mould at high pressure, and the resulting composite is cured under controlled conditions. Injection moulding is an ideal choice for producing complex composite structures with tight tolerances.
Bulk moulding compound is typically used for the injection moulding process, which involves heating the compound and injecting it into a heated mould. The mould is then held under pressure until the resin has cured. While the process is suitable for producing relatively small components with short cycle times, the high cost of tooling means that it is only suitable for medium to high volume production. Overall, injection moulding is an excellent choice for manufacturing complex composite structures with tight tolerances, making it a popular option for a range of industries.
Resin Transfer Moulding
Resin transfer moulding (RTM) is a closed-mould process used for manufacturing composite materials. Dry fibres or pre-impregnated fabrics are placed in a two-part mould, which is then closed. Reactive resin is mixed and injected into the mould under pressure. Pressure is maintained until the resin has cured and the part is removed. This process is ideal for producing medium-to-large composite structures with complex shapes.
The vacuum-assisted resin transfer moulding (VARTM) is a variant of the process in which vacuum is applied to the closed mould, allowing resin to be injected under low pressure. Structural reaction injection moulding (SRIM) is another variant of the process, which uses highly reactive resins that do not require heating to cure, although the mould is often heated to reduce cycle time. The process is suitable for complex, highly-loaded parts and is used in a wide range of industries.
Vacuum Infusion
Vacuum infusion is a manufacturing process for composite materials that involves placing dry fibres or pre-impregnated fabrics in a mould. A vacuum bag is then placed over the mould, and the air is removed to create a vacuum. Resin is then injected into the mould, and the composite is cured under controlled conditions. Vacuum infusion is ideal for producing high-quality, low-weight composite structures with complex shapes.
Filament Winding
Filament winding is a manufacturing process for composite materials that involves winding dry fibres or pre-impregnated fabrics around a mandrel or mould. The fibres are then impregnated with resin and cured under controlled conditions. Filament winding is ideal for producing cylindrical or tubular composite structures, such as pipes and tanks, with high strength-to-weight ratios.
Pultrusion
Pultrusion is a continuous manufacturing process for composite materials. In this process, dry fibres or pre-impregnated fabrics are pulled through a heated die, where they are impregnated with resin and cured under controlled conditions. Pultrusion is ideal for producing long, continuous composite structures, such as beams and profiles, with high strength-to-weight ratios.
Prepreg
Prepreg is a pre-impregnated composite material that is manufactured using a variety of techniques, including wet lay-up, spray-up, and filament winding. Prepreg materials are stored in a cooled state until they are ready for use. When heated, the resin in the prepreg material cures, producing a high-quality composite structure with consistent properties. Prepreg materials are ideal for producing high-performance composite structures that require exceptional strength and durability.
Composite materials in Aerospace
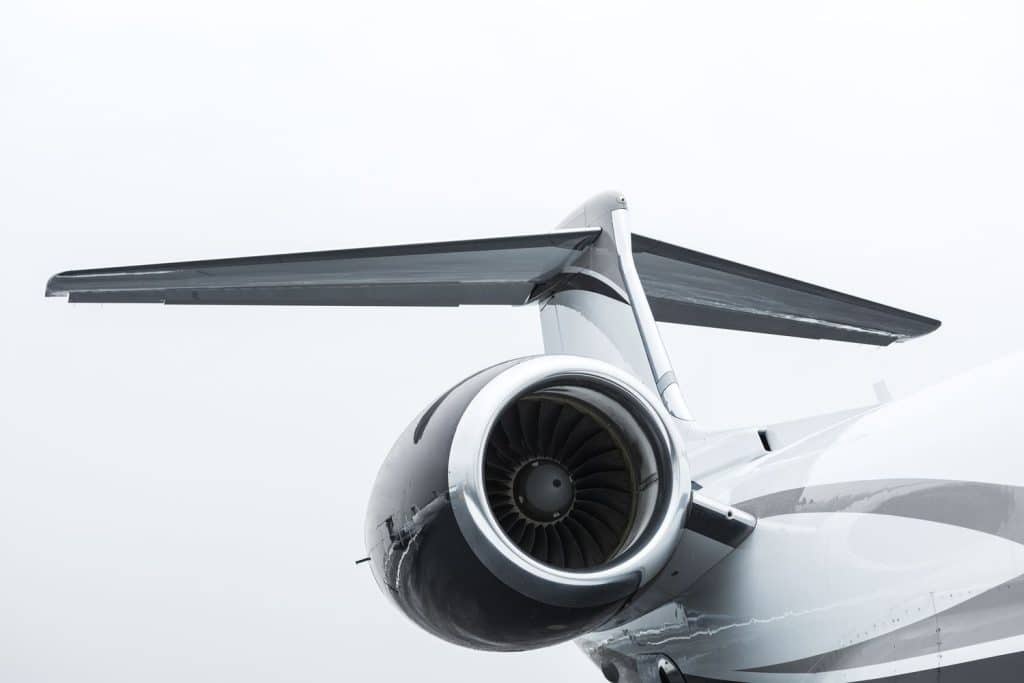
The aerospace industry has been a pioneer in the use of composite materials due to their high strength-to-weight ratio. The use of composites in aircraft has increased significantly over the years, and now most of the structural components of an aircraft are made of composite materials.
Advantages of composite materials in aerospace
The use of composites in aerospace has many advantages, including:
- High strength-to-weight ratio
- High fatigue resistance
- Corrosion resistance
- Reduced maintenance costs
- Improved fuel efficiency
Applications of composites in aerospace
Composites are used in various applications in the aerospace industry, including:
- Fuselage and wings of commercial airliners
- Rotors and blades of helicopters
- Engine nacelles and fan blades
Interior components, such as seats and overhead bins
Composite materials in the Automotive Industry
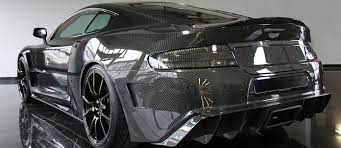
The automotive industry has also started to embrace the use of composite materials due to their lightweight and high stiffness. The use of composites in automobiles can lead to significant fuel savings and reduced carbon.
Benefits of using composites in the automotive industry
The use of composites in the automotive industry has many benefits, including:
- Lightweight
- High stiffness
- Reduced fuel consumption
- Lower carbon emissions
- Improved crash safety
Applications of composites in the automotive industry
Composites are used in various applications in the automotive industry, including:
- Body panels and parts
- Suspension components
- Wheels and rims
- Interior components, such as dashboards and door panels
Composite materials in the Sporting Goods Industry
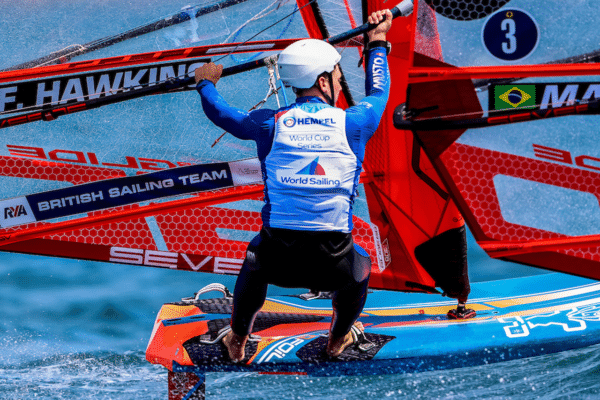
The use of composite materials in the sporting goods industry has also grown significantly over the years. Composites provide many benefits to athletes, such as increased performance and reduced injury risk.
Advantages of composites in sporting goods
The advantages of using composites in sporting goods include:
- Lightweight
- High strength and stiffness
- Improved durability
- Reduced vibration and shock
- Improved aerodynamics
Applications of composites in sporting goods
Composites are used in various applications in the sporting goods industry, including:
- Tennis rackets and golf clubs
- Bicycles and helmets
- Skis and snowboards
- Surfboards and paddleboards
Future developments in composite materials
The development of new composite materials is ongoing, and researchers are continually exploring ways to improve their performance properties. Some of the future developments in composite materials include:
- Nanocomposites
- 3D printing of composites
- Smart composites with sensors and actuators
- Biodegradable composites
Use of Composite Materials in the Medical Industry
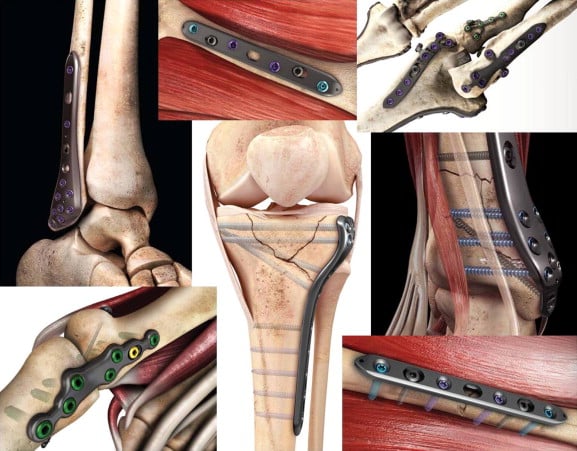
Composite materials are finding increasing use in the medical industry. Some of the applications of composite materials in the medical industry include:
Orthopaedic Implants
Orthopaedic implants are used to replace damaged or diseased bones and joints. Composite materials such as carbon fibre reinforced polymers and ceramic matrix composites are being used to manufacture orthopaedic implants. These materials offer superior strength, durability, and biocompatibility.
Dental Implants
Composite materials are also used in dental implants. The most commonly used composite material for dental implants is zirconia. Zirconia implants offer excellent biocompatibility, strength, and durability.
Prosthetics and Orthotics
Composite materials are also used to manufacture prosthetics and orthotics. Carbon fibre reinforced polymers and fiberglass are commonly used to manufacture prosthetic limbs and braces. These materials offer excellent strength, durability, and lightweight properties.
Medical Imaging
Composite materials are also used in medical imaging. Composite materials such as carbon fibre reinforced polymers are used to manufacture X-ray tables, CT scanner beds, and MRI equipment. These materials offer excellent strength and lightweight properties, making them ideal for use in medical imaging equipment.
Surgical Instruments
Composite materials are also finding use in the manufacture of surgical instruments. Carbon fibre reinforced polymers and ceramic matrix composites are being used to manufacture surgical instruments. These materials offer superior strength, durability, and lightweight properties.
Conclusion
Composite materials are changing the way we design and manufacture products in various industries, from aerospace to sporting goods. The unique properties of composites, such as their high strength-to-weight ratio, durability, and flexibility, make them a preferred choice for many applications. As technology continues to advance, we can expect to see even more innovative developments in composite materials in the future.
FAQ
Are composite materials more expensive than traditional materials?
Composite materials can be more expensive than traditional materials due to the manufacturing process and specialized equipment required. However, their unique properties and benefits often justify the cost.
Can composite materials be recycled?
Yes, some composite materials can be recycled. However, the recycling process can be challenging due to the different types of materials used in composites.
What is the difference between PMCs, MMCs, and CMCs?
The main difference between PMCs, MMCs, and CMCs is the type of matrix material used. PMCs use a polymer matrix, MMCs use a metal matrix, and CMCs use a ceramic matrix.
Can composite materials be repaired if they are damaged?
Yes, composite materials can be repaired if they are damaged. However, the repair process can be complex and requires specialized knowledge and equipment.
How long do composite materials last?
The lifespan of composite materials depends on the application, environment, and maintenance. However, properly designed and maintained composites can last for many years.