One of the most common and versatile processes used in the manufacturing industry is CNC Machining. You might be surprised to learn that the roots of CNC machining can be traced back to the 1950s, when innovative manufacturers at MIT made a groundbreaking discovery that revolutionized the production process. By harnessing the power of computers for rapid prototyping and manufacturing, they were able to drastically reduce the time required to create parts, from 8 hours down to just 15 minutes. This watershed moment paved the way for the birth of CNC machining as we know it today.
Since its inception, CNC machining has undergone remarkable advancements and has reshaped the world of engineering. It has become the go-to method of digital manufacturing across a wide range of technical industries, offering unprecedented precision and efficiency. From aerospace to automotive, electronics to healthcare, CNC machining has made its mark as an indispensable tool in the pursuit of innovation and excellence.
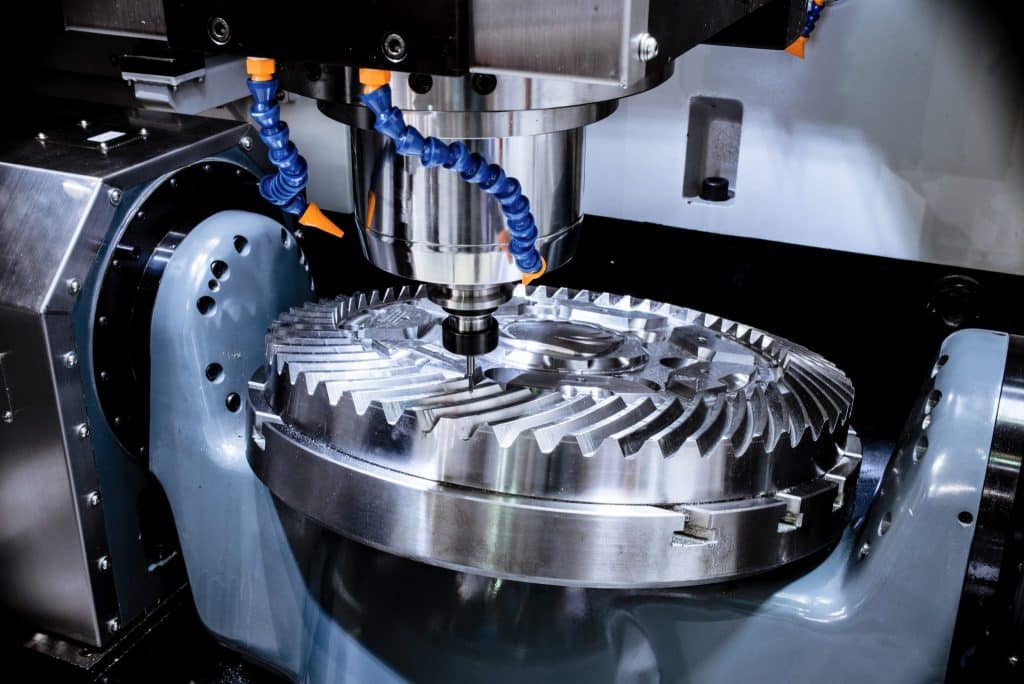
What is CNC Machining?
CNC machining, or Computer Numerical Control machining, is a precise and versatile form of subtractive manufacturing. It involves using computer-controlled machinery to remove material from a solid blank, shaping it into the desired final product. This process is guided by a set of programmed instructions, known as the part program, which specifies the cuts and operations to be performed by the CNC machine.
By converting a digital model of the part into a sequence of computer instructions, CNC machining offers exceptional precision and repeatability. The programmed instructions control the movements and actions of the machining tools, enabling complex shapes and tight tolerances to be achieved with ease. CNC machining is not limited to specific materials and can work with metals, metal alloys, plastics, wood, stone, and more.
With the ability to automate various tasks and follow programmed instructions, CNC machines streamline production processes and deliver consistent quality. This makes CNC machining a popular choice across many industries. It has revolutionized manufacturing by providing faster production times, reduced error rates, and the capability to create intricate and customized parts.
Components of CNC Machine
A CNC machine comprises various components that work together to enable precise control and automation in the manufacturing process.
- Central Processing Unit (CPU): The CPU serves as the control centre of the CNC system. It receives the part program stored in the memory and decodes it, converting the data into position and velocity control signals. The CPU oversees the movement of the spindle and control axes, ensuring they align with the programmed data and correcting any discrepancies. Input devices include magnetic tape readers, punch tape readers, and computers connected via RS-232-C communication.
- Machine Control Panel: The machine control panel provides a direct interface between the operator and the CNC system. It displays instruments for controlling, monitoring, and managing the machine. Before executing a program, the machine must be prepared, which involves loading the required part program into the system memory and establishing a correct reference point. The CNC system then controls the motion of the axes and functions of the spindle or tool based on the stored part program.
- Machine Tool: The machine tool encompasses various types of machinery controlled by CNC. It typically consists of a slide table and a spindle, which are responsible for controlling the position and speed of the machining process.
- Programmable Logic Controller (PLC): The PLC is an industrial solid-state computer that interfaces with the CNC system. It follows pre-programmed rules, makes logic-based decisions, and controls the inputs and outputs of the system. PLCs help minimize manual operations and can withstand harsh environmental conditions.
- Servo Control Unit: The servo control unit ensures precise position control by receiving position feedback signals from feedback devices. It generates appropriate command values that interface with the axes and spindle motors, enabling accurate movement and control.
- Feedback Devices: These devices, also known as measuring systems, consist of position and speed transducers that act as sensors. They monitor the current position of the cutting tool in real-time, providing feedback for precise control and positioning.
- Display Unit: The display unit serves as an interactive device between the operator and the CNC machine. It provides a visual interface to monitor the status of programs, commands, and other necessary data. The display unit is also helpful for maintenance and installation purposes, as it can present machine parameters, program controller logic diagrams, error messages, and diagnostic data.
Terminologies used in CNC Machining
To understand CNC machining fully, it’s essential to become familiar with some common terminologies:
Computer-Aided Design (CAD): CAD refers to the use of computer software to create detailed designs and models of parts or products. CAD software allows engineers and designers to precisely define the geometry, dimensions, and specifications of the desired component.
Computer-Aided Manufacturing (CAM): CAM software is used to convert CAD models into machine-readable instructions. It generates toolpaths and machining strategies based on the design specifications, ensuring efficient and accurate production. CAM software takes into account factors such as cutting tools, material properties, and desired surface finish.
Distributed Numerical Control (DNC): DNC is a system that enables the transfer of programs and data between a central computer and multiple CNC machines. It allows for centralized program storage, editing, and retrieval, ensuring consistency and synchronization across different machines in a manufacturing facility.
Manufacturing Data Collection (MDC): MDC involves the collection and analysis of real-time data from CNC machines during the manufacturing process. This data includes information about cycle times, machine utilization, tool life, and production quantities. MDC systems help monitor and optimize production performance, improve efficiency, and identify areas for process improvement.
G-code: G-code, short for Geometric code, is an alphanumeric language that tells the CNC machine how to move and operate. Each line of G-code contains instructions for specific movements, such as positioning the tool or controlling the spindle.
In G-code, the X, Y, and Z references represent the different axes of movement. The X-axis corresponds to horizontal movement, the Y-axis to vertical movement, and the Z-axis to depth or depth-of-cut. The numerical values assigned to each axis determine the precise position or distance of movement. And N refers to the line number.
M-code: M-code commands are used to control auxiliary functions and operations of CNC machines, such as tool changes, coolant activation, spindle control, and machine tool positioning. M-code commands work in conjunction with G-code instructions to coordinate and execute specific machine actions.
How Does CNC Machining Work?
Design and CAD/CAM Preparation: The process begins with designing the parts using computer-aided design (CAD) software. The 3D model defines the dimensions and specifications of the final part. If the CAD and computer-aided manufacturing (CAM) software are from the same product family, the CAD files can be directly used. Otherwise, the CAD files are imported into CAM software. CAM software prepares the model for fabrication by checking for errors and generating a CNC program for manufacturing.
CNC Programming: The CNC program, created by the CAM software, consists of a set of coordinates that guide the cutting head or tools during the machining process. It contains instructions about cutting trajectories, tooling, and other parameters. The program is typically written using G-code and M-code, which are standard programming languages for CNC machines.
Parameter Selection: Before starting the machining process, appropriate parameters such as cutting speed, voltage, and RPMs need to be selected. These parameters depend on the geometry of the part, available machinery, and tooling. Choosing the right parameters ensures optimal cutting performance and accuracy.
Nesting and Material Usage: The CAM software determines the nesting, which involves arranging and orienting the parts relative to the raw material to maximize material usage. Efficient nesting reduces material waste and improves production efficiency.
Code Translation and Machine Execution: The software translates all the design, programming, and parameter information into machine-readable codes, namely M-code and G-code. These codes provide instructions to the CNC machine, controlling its movements, tool changes, and other operations. The CNC machine executes the codes and performs the cutting, shaping, and other manufacturing processes automatically.
CNC machines are powered by computers that automate, monitor, and control the movements of the industrial machines. In large industrial plants, the computer is typically integrated into the machines, while hobbyist machines often have an external computer attachment. The specific movements executed by the CNC machine depend on the type of machine being used, whether it’s a milling machine, lathe, router, or other specialized CNC equipment.
Common Types of CNC machine
CNC machining encompasses a range of specialized machines, each designed for specific applications. Here are some of the common types of CNC machines:
CNC Milling Machines: CNC milling is widely used and known for its accuracy and precision. These machines have built-in tools for drilling and cutting. The computer controls the movement of the cutting tools, allowing for precise material removal. There is multi-axis in CNC Machining, 3-axis and 5-axis. What sets apart a 3-axis CNC machine from a 5-axis CNC machine? Well, the key distinction lies in their capabilities to orient and maneuver the cutting tool along multiple axes. A 3-axis CNC machine can move its cutting tool along the X, Y, and Z axes. On the other hand, a 5-axis machine has the ability to move the cutting tool along the X, Y, Z, A, and B axes.
CNC Lathe Machines: CNC turning is the process where the material is rotated while cutting tools shape it. CNC lathe machines have a central lathe that manipulates and moves the material according to the programmed instructions. This type of machine is ideal for turning cylindrical or symmetrical parts.
CNC Plasma-Cutting Machines: Used for cutting materials, CNC plasma-cutting machines employ a high-powered plasma torch. The intense heat generated by the torch enables it to cut through robust materials like metal. The computer controls the movement of the torch, allowing for precise and efficient cutting operations.
CNC Laser-Cutting Machines: Just like plasma-cutting machines, Laser-cutting CNC machines are also designed to cut through resilient materials. But these machines employ lasers instead of plasma torches to carry out the cutting process. Laser-cutting CNC machines are known for their exceptional cutting precision, although they may not possess the same level of cutting power as plasma torches.
CNC Electric Discharge Machines: Also known as spark CNC machines, these specialized CNC machines use electrical sparks to shape materials. A top and bottom electrode apply controlled electrical discharges to reshape the material. CNC electric discharge machines are particularly useful for machining intricate and delicate parts, such as those required in the mould and die industry.
4 Important Feature of CNC Machining
Great for creating large quantities of parts: CNC machining excels at mass production due to its ability to replicate parts with exceptional precision and consistency. Once the CNC program is set up, the machine can produce a large volume of parts with minimal human intervention, resulting in improved efficiency and cost-effectiveness.
Can work with many materials: CNC machines can handle a wide range of materials, including metals like aluminium, steel, as well as plastics, wood, and composites. This versatility makes CNC machining suitable for diverse applications across industries such as automotive, aerospace, electronics, and healthcare.
Can create parts quickly: CNC machining offers rapid production capabilities, allowing for the quick turnaround of parts. The automation and high-speed operation of CNC machines enable efficient material removal and precise shaping, reducing production time compared to traditional machining methods.
Highly accurate: Precision is a hallmark of CNC machining. The computer-controlled nature of CNC machines ensures consistent accuracy and repeatability, resulting in parts with tight tolerances and minimal errors. This level of precision is crucial in industries where component fit, functionality, and quality are critical, such as aerospace and medical device manufacturing.
Conclusion
CNC machining has revolutionised the manufacturing industry with its advanced technology and numerous benefits. By tracing its roots back to the 1950s and highlighting its transformative impact on engineering. Moving on to understand what CNC machining entails, we learned about its subtractive manufacturing process, where material is removed to create intricate parts with high precision. The components of a CNC machine, including the CPU, input devices, machine control panel, and feedback devices, were discussed to demonstrate the intricate workings of this technology. We also delved into the terminologies used in CNC machining, such as CAD, CAM, DNC, MDC, G-code, and M-code, which are essential for programming and controlling the machines. Understanding how CNC machining works, we explored the design process, CAM software, parameter selection, and the translation of instructions into machine-readable code. Additionally, we explored the common types of CNC machines, including milling, lathe, plasma-cutting, laser-cutting, and electric discharge machines, each with its unique capabilities and applications. Finally, we emphasized the importance of CNC machining, such as its ability to handle large production quantities, work with various materials, achieve fast turnaround times, and deliver exceptional accuracy. With these insights, it is evident that CNC machining continues to be a vital technology driving efficiency, productivity, and innovation in modern manufacturing processes.