Metal fabrication has been an integral part of various industries, from automotive to construction, for decades. Ensuring the longevity and performance of metal components is crucial, and one way to achieve this is through inorganic coatings. In this article, we’ll delve into the world of inorganic coating in metal fabrication, exploring their benefits, types, and applications. Let’s get started.
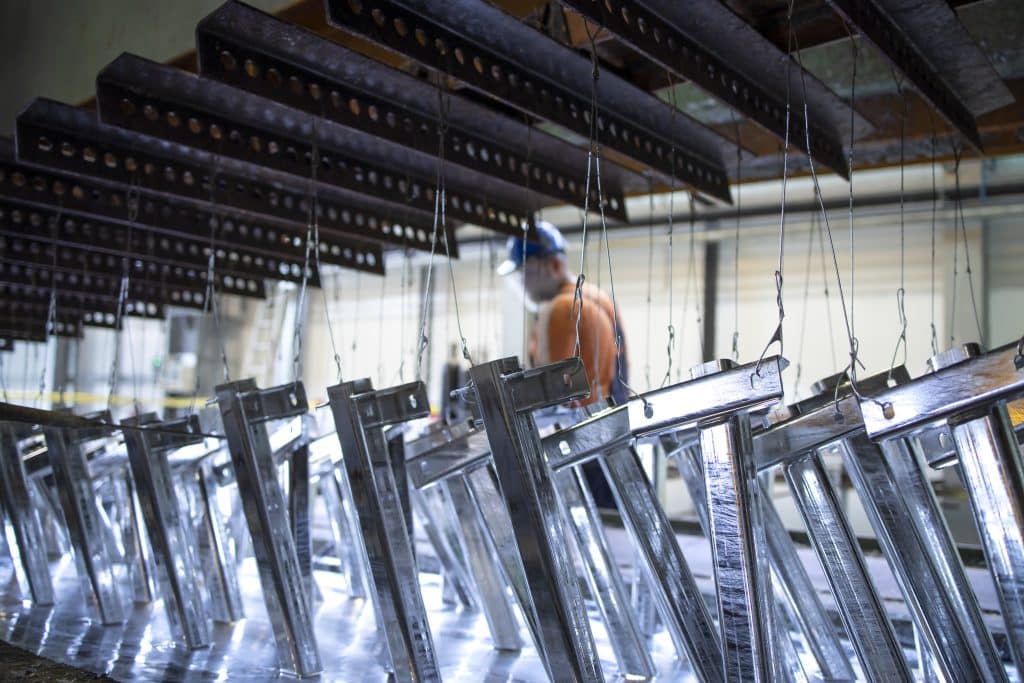
Understanding Inorganic Coating
What Are Inorganic Coatings?
Inorganic coatings, also known as non-metallic coatings, are a protective layer applied to metal surfaces to enhance their properties. These coatings are composed of minerals, ceramics, and other non-metallic materials, making them distinct from organic coatings like paints and varnishes.
How Do Inorganic Coatings Work?
Inorganic coatings create a barrier between the metal substrate and the surrounding environment. They serve as a shield against corrosion, wear and tear, and other forms of degradation. By inhibiting the direct contact between the metal and potentially harmful agents, they extend the lifespan of metal components.
Types of Inorganic Coating
1. Anodizing
Anodizing is a widely used inorganic coating method , which involves creating a thick layer of oxide on the surface of aluminium or its alloys. The oxide layer enhances the corrosion resistance, wear resistance, and aesthetic appearance of the aluminium surface. Anodizing can also create various colours and patterns on the aluminium surface by using different electrolytes and additives.
2. Galvanization
Galvanization is a process of coating metal with a layer of zinc to protect it from corrosion. Zinc acts as a sacrificial anode that corrodes preferentially to the metal substrate, thus preventing rusting. Galvanization is commonly used for steel fabrication, especially for outdoor structures and pipes.
3. Phosphate Coatings
Phosphate coatings are used to prepare the metal surface for painting or other organic coatings. They enhance adhesion and provide a degree of corrosion resistance. These coatings are often used in the automotive industry.
4. Ceramic Coatings
Ceramic coating is a process of applying an inorganic coating made from metal oxides or carbides that provide excellent resistance to wear, heat, and corrosion. Ceramic coatings can also improve the thermal efficiency, electrical conductivity, and lubricity of the metal surface. Ceramic coatings are often used for high-temperature applications, such as gas turbines, jet engines, and rocket nozzles.

6 Benefits of Inorganic Coating
1. Corrosion Resistance
Inorganic coatings are highly effective at preventing corrosion, making them essential for metal components exposed to moisture and harsh weather conditions.
2. Improved Aesthetics
Coatings like anodizing can enhance the appearance of metal surfaces, making them more appealing and suitable for various applications.
3. Reduced maintenance costs
Inorganic coatings can help to extend the lifespan of metal components, which can reduce the need for frequent maintenance and repairs. For example, a study by the National Association of Corrosion Engineers found that galvanizing steel can increase its lifespan by up to 50 years. This can lead to significant savings in maintenance costs over the life of the asset.
4. Improved electrical conductivity
Certain inorganic coatings, such as gold plating, can improve the electrical conductivity of metal surfaces. This can be beneficial for applications in electronics and telecommunications. For example, gold plating is often used on electrical contacts and connectors to ensure reliable electrical connections.
5. Reduced friction and wear
Inorganic coatings can reduce friction and wear on metal surfaces, which can improve performance and extend the lifespan of components. For example, ceramic coatings are often used on cutting tools and other wear-prone components to improve their performance and durability.
6. Enhanced fire resistance Certain inorganic coatings, such as ceramic coatings, can enhance the fire resistance of metal components. This can be important for applications in hazardous environments, such as chemical plants and power plants. For example, a study by the National Fire Protection Association found that ceramic coatings can increase the fire resistance of steel beams by up to 2 hours.
Applications of Inorganic Coatings
1. Automotive Industry
Inorganic coatings are used extensively in the automotive industry to protect various metal parts from corrosion and enhance their appearance.
2. Building and Construction
Galvanization is a common choice for structural steel components in construction projects, as it provides long-lasting protection against the elements.
3. Aerospace
The aerospace industry relies on inorganic coatings to ensure the durability and performance of critical components, particularly in extreme conditions.
4. Medical devices
Inorganic coatings are used on medical devices, such as implants and surgical instruments, to improve their biocompatibility and corrosion resistance.
5. Food processing equipment
Inorganic coatings are used on food processing equipment to prevent contamination and improve sanitation.
6. Power generation Inorganic coatings are used on power generation equipment, such as turbines and heat exchangers, to protect them from corrosion and wear.
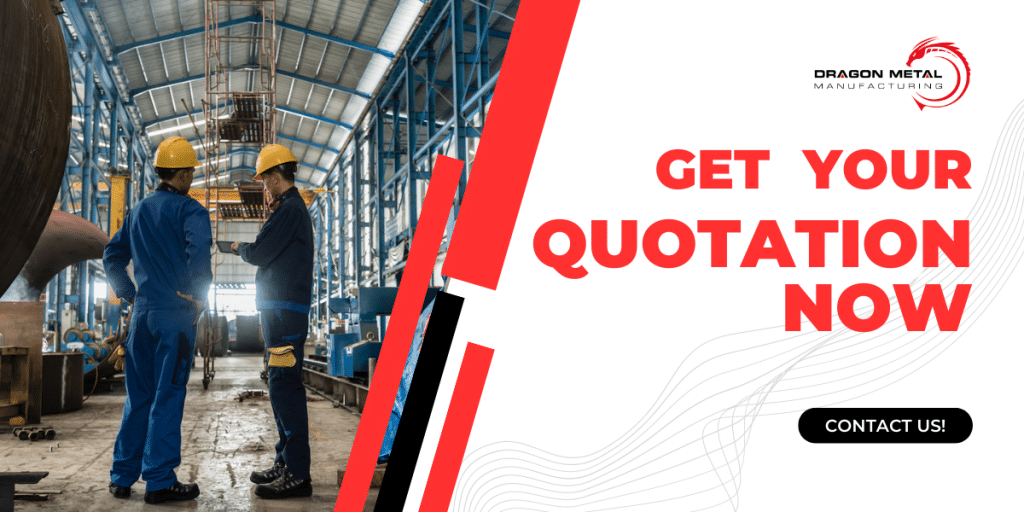
Conclusion
Inorganic coatings play a pivotal role in the world of metal fabrication. They provide an effective shield against corrosion, enhance aesthetics, and offer high-temperature resistance. Whether in the automotive, construction, or aerospace industry, the use of inorganic coatings is essential to ensure the longevity and performance of metal components.