The automotive industry is one of the most demanding and competitive sectors in the world, requiring high-quality, durable, and reliable components for various applications. One of the methods that can produce such parts is forging, a process that involves shaping metal using compressive forces at high temperatures. Forging can create parts that are stronger, lighter, and more resistant to wear and tear than other methods, such as casting or machining.
In this blog post, we will explore the basics of forging, the most common materials used in forging auto parts, the different forging processes used in making automotive forging parts, and some examples of automotive forged metals parts. We will also discuss the benefits and challenges of forging for the automotive industry, and how it can contribute to automotive excellence.
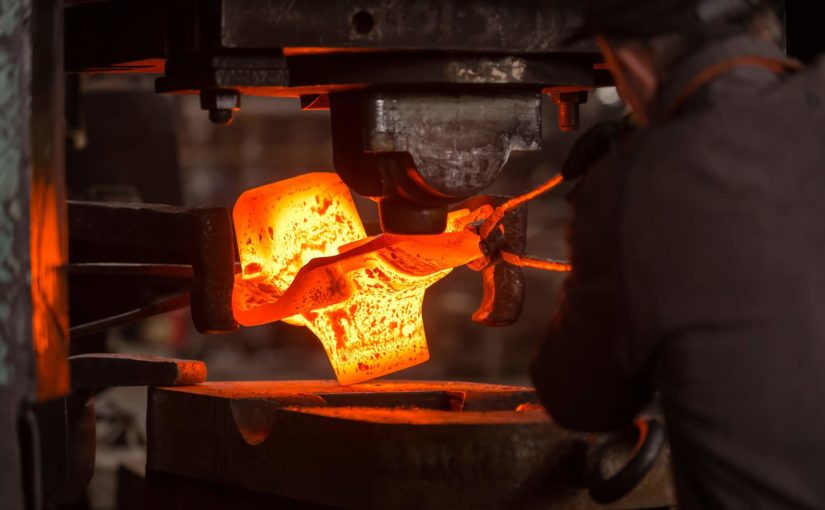
Overview of Forging Metal Parts
Forging is a metalworking process that dates back to ancient times, when blacksmiths used hammers and anvils to shape metal into tools and weapons. Today, forging is done using sophisticated machines and equipment that can apply precise and controlled forces to metal at high temperatures, ranging from 900°C to 1200°C.
Forging can be classified into two main categories: hot forging and cold forging. Hot forging is done at temperatures above the recrystallization point of the metal, which allows the metal to deform plastically without cracking or breaking. Cold forging is done at temperatures below the recrystallization point of the metal, which increases the strength and hardness of the metal, but also requires more force and energy.
Forging can also be classified according to the degree of contact between the metal and the dies (the tools that shape the metal). There are three main types of forging: open die forging, closed die forging, and roll forging. Open die forging is done by placing the metal between two flat or contoured dies that do not enclose the metal completely, allowing the metal to flow freely in some directions. Closed die forging is done by placing the metal in a cavity formed by two or more dies that completely enclose the metal, creating a near-net-shape part with minimal waste. Roll forging is done by passing the metal through two or more rotating rolls that reduce the thickness and increase the length of the metal.
Most Common Materials Used in Forging Metal Parts for Auto
The choice of material for forging auto parts depends on several factors, such as the desired properties, performance, cost, availability, and environmental impact of the material. Some of the most common materials used in forging auto parts are:
Aluminium
Aluminium is a lightweight, corrosion-resistant, and recyclable material that can be forged into various shapes and sizes. Aluminium forgings are widely used in automotive applications, such as wheels, suspension components, engine parts, chassis parts, and body panels. Aluminium forgings can offer advantages such as reduced weight, improved fuel efficiency, lower emissions, increased safety, and enhanced aesthetics.
Steel
Steel is a strong, durable, and versatile material that can be forged into complex and intricate shapes. Steel forgings are commonly used in automotive applications that require high strength, toughness, wear resistance, and fatigue resistance, such as crankshafts, connecting rods, gears, axles, bearings, and pistons. Steel forgings can offer advantages such as increased performance, reliability, durability, and longevity.

Process Used in Making Automotive: Forging Metal Parts
The choice of forging process for making automotive forging parts depends on several factors, such as th e type of material, the shape and size of the part, the production volume, the quality requirements, and the cost considerations. Some of the most common forging processes used in making automotive forging parts are:
Closed Die Forging
Closed die forging is a process that involves placing a preheated metal billet (a semi-finished piece of metal) in a cavity formed by two or more dies that completely enclose the metal. The dies are then pressed together with high force, causing the metal to fill the cavity and take the shape of the dies. The excess metal is squeezed out through flash lines (gaps between the dies), which are later trimmed off. Closed die forging can produce near-net-shape parts with high dimensional accuracy, surface finish, and mechanical properties. Closed die forging is suitable for producing complex and intricate shapes with fine details, such as gears, valves, and flanges. Closed die forging is also suitable for producing high-volume parts with consistent quality and low scrap rate.
Open-Die Forging
Open-die forging is a process where the metal part is heated and placed between two flat or contoured dies that are not completely closed. The dies hammer or press the metal part until it reaches the desired shape and size. Open-die forging is suitable for producing large and simple parts such as shafts, rings, and cylinders. Open-die forging can also be used to pre-form the metal part before it undergoes another forging process.
Differences Between Open-Die and Closed-Die Forging
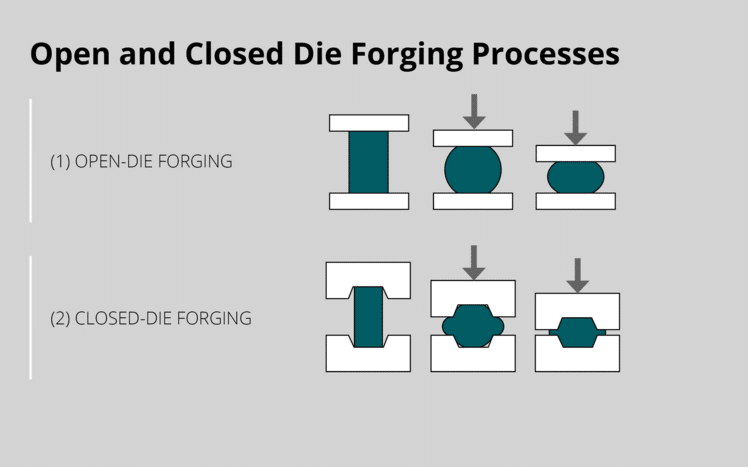
One of the main differences between open-die and closed-die forging is the shape and size of the dies used in the process. Open-die forging uses flat or contoured dies that do not completely enclose the metal, while closed-die forging uses dies that have a cavity or impression that matches the shape of the part.
Another difference is the dimensional accuracy and surface finish of the forged parts. Open-die forging produces parts with low dimensional accuracy and surface finish, as the metal is free to flow in all directions. Closed-die forging produces parts with high dimensional accuracy and surface finish, as the metal is confined within the die cavity. A third difference is the complexity and cost of the forging process. Open-die forging is simpler and cheaper than closed-die forging, as it requires less tooling and machining. However, open-die forging is limited by the size and shape of the hammer and anvil and cannot produce complex parts. Closed-die forging is more complex and expensive than open-die forging, as it requires more tooling and machining. However, closed-die forging can produce complex parts with intricate details and features.
Roll Forging
Roll forging is a process that involves passing a preheated metal billet through two or more rotating rolls that reduce the thickness and increase the length of the metal. The rolls can have flat or grooved surfaces that impart the desired shape and profile to the metal.
Roll forging can produce parts with uniform cross-sections and smooth surfaces. Roll forging is suitable for producing simple and symmetrical shapes with long lengths, such as bars, rods, and shafts. Roll forging is also suitable for producing low-to-medium volume parts with low tooling cost and high productivity.
Upset Forging
This process uses a press or a hammer to increase the diameter of a metal rod or bar by reducing its length. The metal is heated to a high temperature and then placed between two flat dies. The dies are then moved towards each other to compress the metal radially. Upset forging is suitable for producing parts with large heads or flanges, such as bolts, screws, and rivets.
Automotive Forged Metal Parts
Some examples of automotive forged metals parts are:
Crankshafts: Crankshafts are the main rotating components of an engine that convert the linear motion of the pistons into rotational motion. Crankshafts are usually forged from steel or alloy steel, as they require high strength, toughness, wear resistance, and fatigue resistance. Forged crankshafts can offer advantages such as improved performance, reliability, durability, and longevity.
Connecting Rods: Connecting rods are the components that connect the pistons to the crankshafts. Connecting rods are usually forged from steel or aluminium, as they require high strength, light weight, and stiffness. Forged connecting rods can offer advantages such as reduced weight, improved fuel efficiency, lower emissions, increased safety, and enhanced aesthetics.
Gears: Gears are the components that transmit power and motion between different parts of a vehicle, such as the engine, transmission, differential, and wheels. Gears are usually forged from steel or alloy steel, as they require high strength, hardness, wear resistance, and noise reduction. Forged gears can offer advantages such as increased performance, reliability, durability, and longevity.
Steering knuckles: These are the parts that connect the steering system to the suspension system. They are responsible for transferring the steering force to the wheels, so they need to be rigid and reliable.
Conclusion
Forging is a metalworking process that can produce high-quality, durable, and reliable parts for various automotive applications. Forging can create parts that are stronger, lighter, and more resistant to wear and tear than other methods, such as casting or machining. Forging can also contribute to automotive excellence by offering benefits such as reduced weight, improved fuel efficiency, lower emissions, increased safety, and enhanced aesthetics. Forging is a process that involves shaping metal using compressive forces at high temperatures. Forging can be classified into two main categories: hot forging and cold forging. Forging can also be classified according to the degree of contact between the metal and the dies: open die forging, closed die forging, and roll forging. Some of the most common materials used in forging auto parts are aluminium and steel. Some of the most common forging processes used in making automotive forging parts are closed die forging and roll forging. Some examples of automotive forged metals parts are crankshafts, connecting rods, and gears.