In an era of rapid technological advancements, automation has emerged as a transformative force in metal manufacturing. Traditional labour-intensive processes have given way to automated systems, revolutionizing the industry. Automation in Metal manufacturing involves the integration of advanced machinery, robotics, and computerized systems to perform tasks previously carried out by humans. This shift has led to significant improvements in productivity, quality control, and overall operational efficiency. In modern sheet metal fabrication facilities, automated systems equipped with precision sensors and actuators can perform complex tasks with remarkable speed and accuracy, increasing production capacity while minimizing errors.
The rise of automation goes beyond individual machines, encompassing the seamless integration of multiple components and systems. Robotic arms, conveyor systems, and data-driven control systems work in harmony to optimize the manufacturing process. Automation not only enhances productivity but also improves safety, quality control, and resource utilization. From small-scale fabrication shops to large industrial facilities, manufacturers are leveraging automation to stay competitive in a dynamic global marketplace. By embracing automation, metal manufacturing is poised to achieve unprecedented levels of efficiency and innovation. Additionally, with this blog we will uncover the wide-ranging benefits of automation, from improved worker safety to cost savings and heightened product quality.
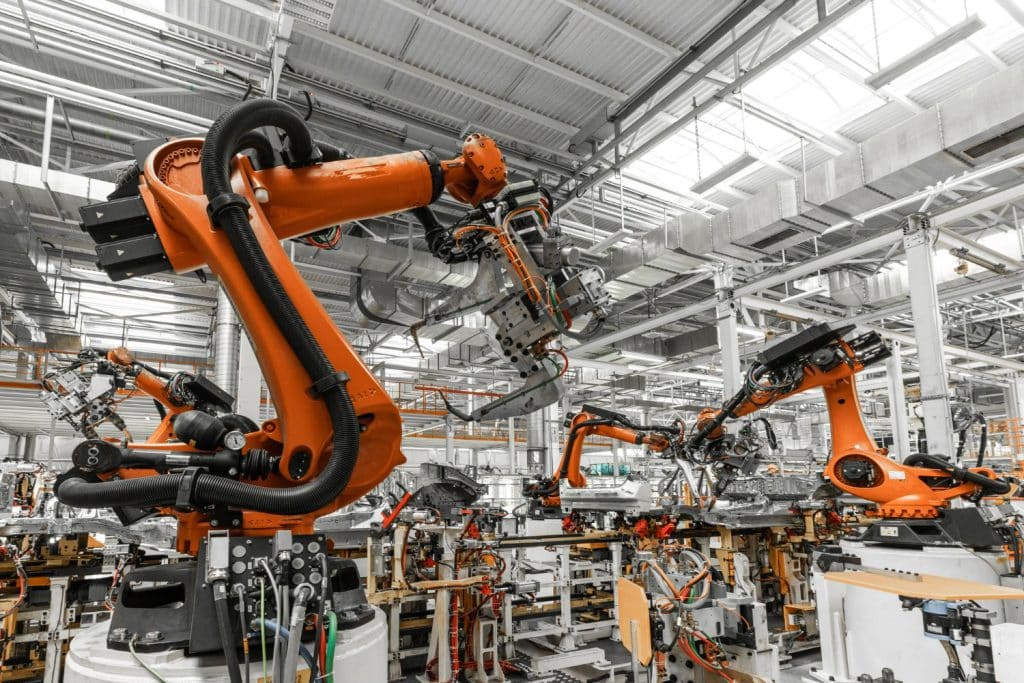
The Power of Automation in Metal Manufacturing
Automation holds immense power in the realm of metal manufacturing, bringing about a paradigm shift in production processes and delivering remarkable advancements. By integrating cutting-edge technologies and computerized systems, automation drives a profound increase in efficiency and productivity. For example, within CNC machining, automated systems enable precise control over cutting tools, resulting in accelerated production rates and reduced material waste. These improvements maximize operational efficiency, propelling the industry forward.
Beyond efficiency gains, automation guarantees consistency and exceptional quality throughout metal manufacturing. Automated systems excel at executing repetitive tasks with remarkable precision, eliminating variations and errors that can occur with human operators. In welding processes, robotic arms equipped with advanced vision systems consistently deliver high-quality welds, ensuring the structural integrity of the final products. This steadfast commitment to quality is particularly crucial in sectors such as aerospace and automotive, where stringent standards and specifications must be met to ensure safety and reliability.
Furthermore, automation streamlines operations and revolutionizes supply chain management within metal manufacturing. Through interconnected systems and real-time data analysis, automated processes optimize crucial aspects such as inventory management, scheduling, and logistics. For instance, integrating an automated inventory tracking system with just-in-time production practices allows manufacturers to minimize inventory holding costs and respond promptly to customer demands. This agile and streamlined approach enhances overall operational efficiency and responsiveness to dynamic market conditions.
3 Types of Automation in Metal Manufacturing
Fixed Automation
Fixed automation refers to the implementation of specialized machinery or equipment designed to perform a specific set of tasks without significant variation. This type of automation is commonly used in high-volume production processes that require repetitive and standardized operations. Fixed automation systems are often designed for dedicated functions and are not easily reprogrammable.
Programmable Automation
Programmable automation involves the use of computer-controlled equipment that can be programmed and reprogrammed to perform various tasks or processes. Unlike fixed automation, programmable automation offers flexibility and adaptability, making it suitable for batch production or customized manufacturing. This type of automation utilizes programmable logic controllers (PLCs) and computer numerical control (CNC) systems to control machinery and perform complex operations.
Flexible Automation
Flexible automation represents the highest degree of adaptability and versatility in metal manufacturing. It combines the advantages of both fixed and programmable automation, allowing for seamless customization and efficient production of various products. Flexible automation systems are designed to handle a wide range of product variations and can be easily reprogrammed or reconfigured to accommodate changes in product design or specifications.
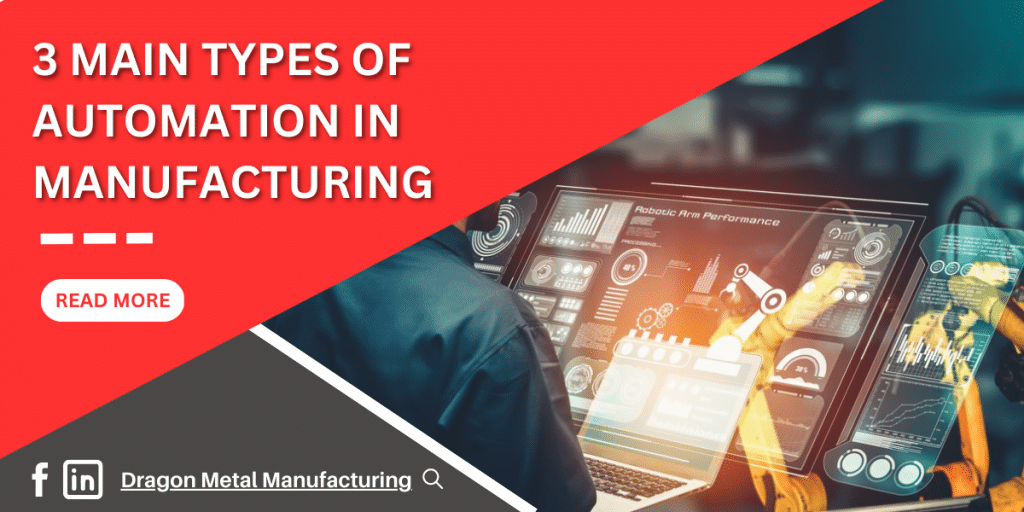
8 Benefits of Automation in Metal Manufacturing
- Mitigating Workplace Hazards: Automation reduces the exposure of workers to hazardous tasks, such as heavy lifting or working in extreme temperatures. For example, in metal manufacturing, automated robotic systems can pour molten metal, eliminating the risk of burns and injuries associated with manual handling.
- Empowering Workers with Safer Environments: By taking on physically demanding or dangerous tasks, automated systems create a safer work environment that empowers workers to focus on higher-level responsibilities. For instance, collaborative robots, also known as cobots, work alongside human operators, enhancing safety and productivity in metal manufacturing.
- Accelerating Production Speed: Automation enables swift production cycles, leading to shorter lead times and the ability to meet rising customer demands. For example, in metal fabrication, automated laser cutting machines can rapidly process metal sheets with precision, reducing production time and increasing throughput.
- Optimizing Resource Utilization: Automated systems efficiently utilize materials, energy, and other resources, minimizing waste and maximizing productivity. In metal stamping, automated press machines precisely control the force and movement, optimizing material usage and minimizing scrap.
- Minimizing Errors and Defects: Through automation, manufacturing processes achieve a high degree of consistency and precision, minimizing the occurrence of human-induced errors and defects. In metal machining, CNC (Computer Numerical Control) systems ensure precise cutting, drilling, and shaping, resulting in high-quality components with tight tolerances.
- Achieving Higher Standards of Quality: Automation enables stringent quality control measures, resulting in products that consistently meet or exceed industry standards and customer expectations. For instance, in metal coating processes, automated systems ensure uniform application of coatings, achieving a superior finish and corrosion resistance.
- Lowering Production Costs: Automation reduces labour costs, minimizes material waste, and optimizes operational efficiency, leading to significant cost savings throughout the manufacturing process. For example, in metal welding, automated robotic systems improve weld quality and reduce rework, resulting in lower labour and material costs.
- Maximizing Return on Investment: Implementing automation generates long-term benefits, including increased production capacity, improved product quality, and enhanced competitiveness, ultimately maximizing the return on investment. Studies have shown that companies that invest in automation technologies experience higher profitability and market growth.

The Imperative Role of Automation in Metal Manufacturing
Navigating Industry Challenges
Addressing Labour Shortages and Skills Gap: Automation plays a crucial role in mitigating the challenges arising from labour shortages and the widening skills gap. By automating repetitive and physically demanding tasks, manufacturers can alleviate their reliance on scarce skilled labour. For instance, in metal manufacturing, the implementation of robotic systems for material handling and assembly reduces the need for manual labour while maintaining high production rates.
Meeting Growing Market Demands: With the increasing demands of the market, manufacturers must find ways to scale their operations and meet customer expectations promptly. Automation provides a solution by enhancing production efficiency and streamlining processes. By adopting automated systems, manufacturers can reduce lead times, improve productivity, and ensure consistent product quality. For example, in the metal fabrication industry, the utilization of automated bending and forming machines enables manufacturers to handle a higher volume of orders without compromising on quality or delivery times.
Paving the Path to Innovation
Leveraging Advanced Technologies: Automation in manufacturing opens doors to leveraging advanced technologies that drive innovation and propel the industry forward. Integration of technologies such as artificial intelligence (AI), Internet of Things (IoT), and data analytics revolutionizes manufacturing processes. For instance, in the realm of metal manufacturing, AI-powered vision systems are employed for quality control, detecting defects, and ensuring precise measurements. These advanced technologies enable real-time monitoring, predictive maintenance, and optimization, fostering innovation and driving efficiency gains.
Accelerating Research and Development: Automation expedites research and development (R&D) efforts, empowering manufacturers to accelerate the pace of innovation. By streamlining testing, prototyping, and iterative processes, automation reduces the time and costs associated with traditional manufacturing approaches. Metal additive manufacturing provides a prime example of how automation accelerates R&D. Automated 3D printers, such as the ones employed by BMW, enable manufacturers to rapidly iterate and refine complex metal components, unlocking new design possibilities and reducing time-to-market.
In partnership with the Fraunhofer Institute for Laser Technology, BMW developed an automated system capable of producing up to 50,000 3D-printed parts per year. This highly automated production line utilizes advanced robotics, intelligent process control, and real-time monitoring to optimize the 3D printing process. By automating the production of metal components, BMW has significantly reduced lead times, improved design iterations, and enhanced the overall efficiency of their R&D efforts. This innovative approach allows BMW to explore complex geometries, lightweight structures, and customized parts, driving advancements in automotive design and manufacturing.
The Rise of Digital Twins and Virtual Simulations: One notable advancement in the realm of innovation is the rise of digital twins and virtual simulations. Digital twins are virtual representations of physical products or systems that mimic their behaviour in real-time. By leveraging digital twins, manufacturers can conduct comprehensive simulations and analyses, allowing them to optimize manufacturing processes, identify potential issues, and make data-driven decisions. For instance, in the aerospace industry, digital twins are used to simulate complex metal structures, predicting their performance under different operating conditions and enabling engineers to optimize designs for enhanced efficiency and safety.
Sustaining Competitiveness in the Global Market
Improving Time-to-Market: In today’s fast-paced business environment, reducing time-to-market is crucial for manufacturers to maintain a competitive edge. Automation plays a vital role in expediting production processes and optimizing operations, enabling manufacturers in the metal fabrication industry to bring their products to market faster. Let’s explore the context of metal surface finishing. Automated surface treatment systems equipped with advanced robotics and precision control mechanisms revolutionize the finishing of metal products. Companies like Midwest Engineered Systems Group have developed innovative automated solutions for surface treatment, utilizing state-of-the-art robotics and intelligent process control. These systems efficiently handle processes such as cleaning, deburring, polishing, and coating, significantly reducing the time required to achieve high-quality finished products. By automating the surface finishing process with the expertise of companies like Midwest Engineered Systems Group, manufacturers can accelerate time-to-market, ensuring quicker product launches and market entry.
Adapting to Changing Customer Needs: Customer demands and preferences are constantly evolving, requiring manufacturers to be agile and adaptable. Automation empowers manufacturers to cater to changing customer needs by providing the flexibility to customize products and rapidly reconfigure production systems. For example, in metal finishing processes, automated systems can apply various surface finishes or coatings based on specific customer requests, allowing manufacturers to meet individual requirements and differentiate themselves in the market. With automation at their core, manufacturers can enhance customer satisfaction and sustain their competitive position in the global market.
Conclusion
The rapid advancement of automation in metal manufacturing has revolutionized the industry, driving significant improvements in efficiency, productivity, and quality. By embracing automation, manufacturers have been able to streamline their operations, reduce labour-intensive tasks, and leverage advanced technologies to unlock new levels of innovation. This transformation has enabled metal manufacturers to stay competitive in a rapidly evolving market landscape.
As we look to the future, the potential of automation in metal manufacturing is boundless. Advancements in technologies such as robotics, AI, and IoT will continue to reshape the industry, bringing about even greater levels of automation and efficiency. With the integration of smart factories, where machines communicate and collaborate seamlessly, manufacturers can achieve unprecedented levels of productivity, flexibility, and responsiveness to customer demands. Additionally, the rise of digital twins and virtual simulations will enable manufacturers to optimize processes, minimize downtime, and make data-driven decisions.