Welcome to the world of aluminium fabrication, where innovation meets versatility. In this blog, we explore the significance of aluminium fabrication in various industries, uncovering its remarkable properties, different grades, and the techniques that bring designs to life. From its rich history and widespread use to its lightweight nature, and workability, aluminium has become a preferred choice in modern manufacturing. Join us on this captivating journey as we delve into the world of aluminium fabrication, discovering its advantages, exploring different grades, and unlocking the techniques that shape the future of industries.
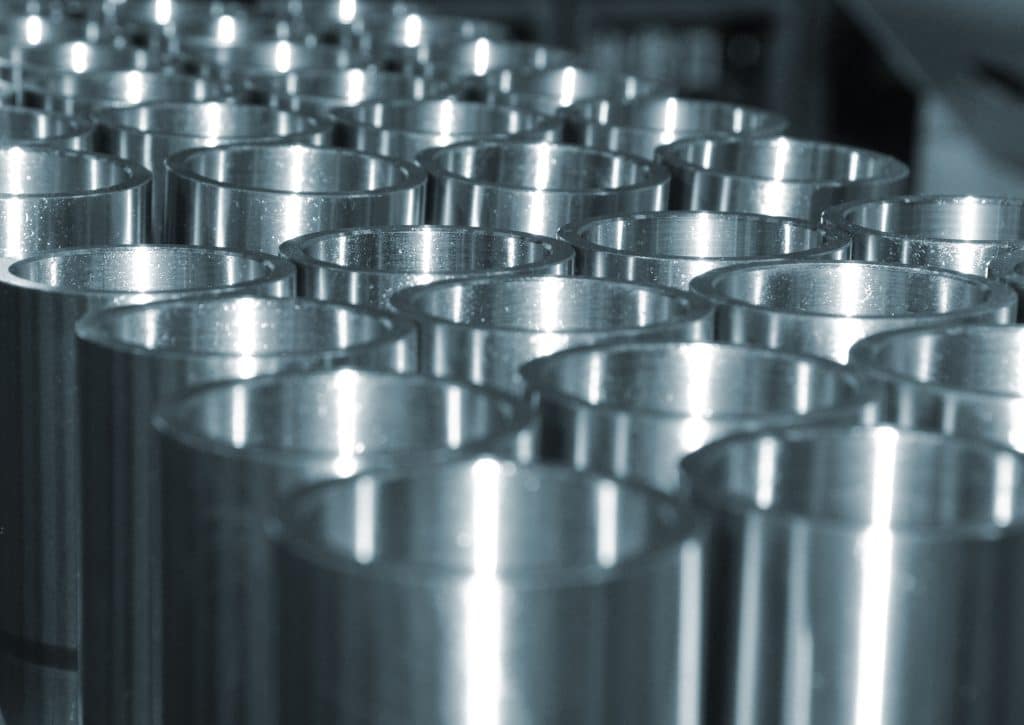
Aluminium’s lightweight characteristic is one of its key advantages, weighing approximately one-third less than stainless steel while maintaining a superior strength-to-weight ratio. This makes aluminium an excellent choice for applications where weight reduction is crucial, such as in the aerospace and automotive industries. For instance, in the aerospace sector, aluminium is widely utilized in the manufacturing of satellite structures, rocket components, and unmanned aerial vehicles (UAVs), enabling enhanced manoeuvrability and fuel efficiency. In the automotive industry, aluminium finds extensive use in the production of lightweight vehicle frames and body panels, leading to improved fuel economy and handling. Renowned electric car manufacturer, Tesla, incorporates aluminium extensively in their vehicle designs to achieve greater range and optimize performance. The widespread adoption of aluminium in these industries demonstrates its pivotal role in achieving lightweight solutions while maintaining structural integrity.
Moreover, aluminium’s remarkable workability contributes to its popularity in fabrication projects. Being a soft metal, aluminium is easily shaped, formed, and manipulated, allowing for intricate designs and complex structures. Its corrosion resistance adds to its appeal, making it suitable for outdoor applications that require durability and long-term performance. One notable example is the construction of architectural facades, where aluminium panels are employed due to their ability to withstand harsh weather conditions while providing an aesthetically pleasing appearance.
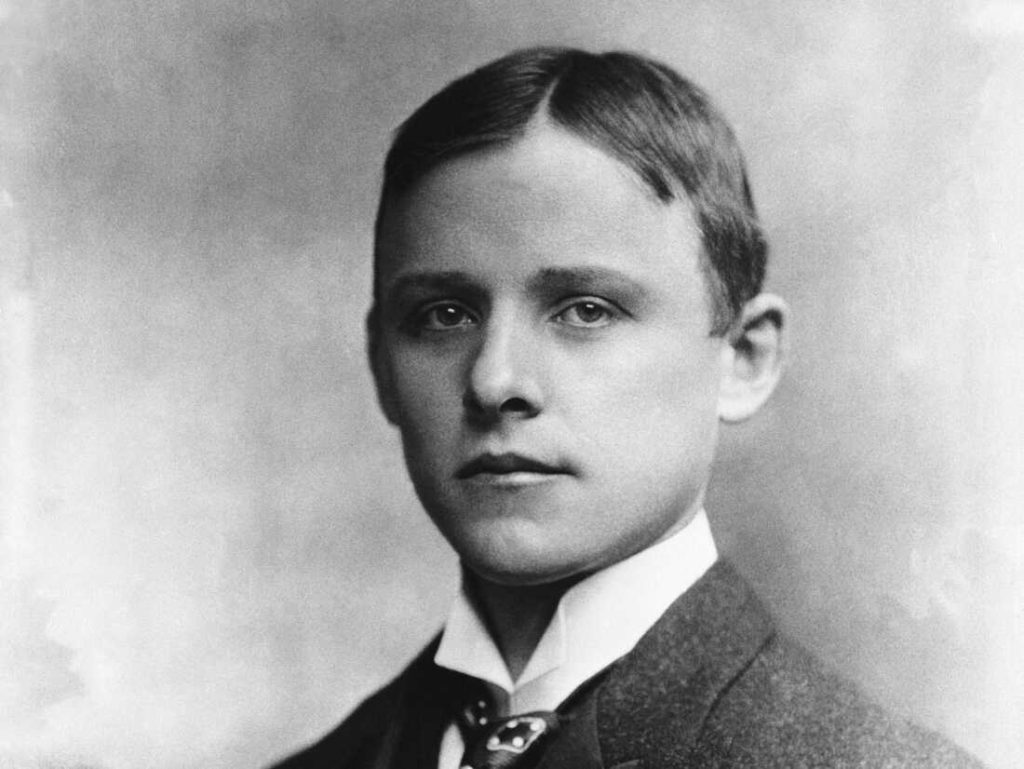
History of Aluminium Fabrication
Discovery and Early Use of Aluminium
The history of aluminium dates back to ancient times, but it wasn’t until the 19th century that the metal was successfully extracted and utilized in fabrication. Aluminium’s discovery is credited to Sir Humphry Davy, who identified it as an element in 1808. However, due to its high reactivity and the challenges associated with its extraction, aluminium remained rare and expensive throughout the early years. In fact, during the mid-19th century, aluminium was considered a precious metal and was even used for decorative purposes. An example of this can be seen in the Washington Monument in the United States, where an aluminium pyramid was placed atop the structure in 1884 to symbolize its value.
Advancements in Aluminium Extraction and Processing Techniques
Significant advancements in aluminium extraction and processing techniques occurred in the late 19th and early 20th centuries, leading to a drastic reduction in production costs and making aluminium more readily available for fabrication. One notable breakthrough was the development of the Hall-Héroult process in 1886, which allowed for large-scale aluminium production by electrolysis of alumina. This revolutionary method, invented by Charles Martin Hall and Paul Héroult independently, marked a turning point in the aluminium industry. With the newfound ability to produce aluminium on a commercial scale, the metal became more accessible and affordable, paving the way for its widespread use in fabrication.
Emergence of Aluminium as a Popular Choice in Fabrication
As aluminium production became more economical, its unique properties and advantages propelled its popularity in the fabrication industry. The lightweight nature of aluminium, weighing a third less than stainless steel while maintaining a high strength-to-weight ratio, caught the attention of designers and engineers. This led to the development of innovative aluminium-based structures and products across various industries. For example, modern architectural marvels such as the Burj Khalifa in Dubai showcase the extensive use of aluminium, demonstrating its aesthetic appeal, versatility, and ability to push the boundaries of fabrication techniques, highlighting the metal’s aesthetic appeal and versatility in fabrication. Over time, aluminium’s corrosion resistance, recyclability, non-toxicity, and ease of workability further solidified its position as a preferred choice for metal fabrication projects.
Properties of Aluminium
Physical properties of aluminium relate to its observable form and structure before any chemical alteration. Understanding these properties is essential for comprehending the characteristics and behaviour of aluminium in various applications.
The physical properties of aluminium include:
- Colour and State: Aluminium is a solid metal with a silvery-white appearance, often with a slight bluish tint. It is non-magnetic and non-lustrous.
- Structure: Aluminium has a face-centred cubic structure that remains stable up to its melting point. This crystal structure contributes to its overall strength and stability.
- Surface: Aluminium surfaces can exhibit high reflectivity, making it suitable for applications requiring reflective surfaces, such as in the construction of solar reflectors or lighting fixtures.
- Hardness: Commercially pure aluminium is relatively soft. However, when alloyed and tempered, aluminium can be significantly strengthened to meet specific mechanical requirements. For example, aluminium alloys used in aerospace applications undergo heat treatment processes to enhance their hardness and strength.
- Ductility: Aluminium possesses high ductility, meaning it can be easily drawn or stretched into thin wires or sheets without breaking. This property is essential in industries that rely on aluminium for applications like electrical wiring and packaging materials.
- Malleability: Aluminium exhibits high malleability, allowing it to be shaped or bent into various forms without cracking or losing structural integrity. This property enables the fabrication of complex and intricate designs in industries such as architecture and automotive manufacturing.
- Thermal Expansion: Aluminium has a moderate thermal expansion coefficient of 23.2, which lies between metals like zinc (higher expansion) and steel (lower expansion). This property is important to consider in applications that involve temperature changes, such as in the construction of bridges or the manufacturing of heat sinks.
- Conductivity: Aluminium is an excellent conductor of both electricity and heat. It has approximately 61% of the electrical conductivity of copper while being significantly lighter. This makes it a preferred choice for electrical transmission lines, heat exchangers, and other applications that require efficient heat and electricity transfer.
- Corrosion Resistance: Aluminium naturally forms a thin, self-protecting oxide layer on its surface, which provides excellent corrosion resistance. This property makes aluminium suitable for outdoor applications where exposure to moisture and environmental elements is common. For instance, aluminium is extensively used in the construction of window frames, automotive parts, and marine equipment.
- Density: Aluminium has a relatively low density of 2.70 g/cm³, making it about one-third the density of steel. This low density contributes to its lightweight characteristic, making it ideal for applications where weight reduction is essential, such as in the aerospace and automotive industries.
- Melting Point and Boiling Point: Commercially pure aluminium has a melting point of approximately 660°C and a boiling point of approximately 2470°C. These values can vary when aluminium is alloyed with other elements, resulting in different melting and boiling points.
Different Grades of Aluminium and Their Uses
A wide range of grades is available when it comes to aluminium, with each grade having its own unique composition and set of properties. These grades are carefully formulated to cater to the specific requirements of different applications, offering varying levels of strength, corrosion resistance, machinability, and other important characteristics. It is essential to have a good understanding of the different grades of aluminium and their respective uses in order to make informed decisions when selecting the most suitable material for specific fabrication projects.
Overview of Aluminium Grades
Grades of aluminium are identified using a four-digit numbering system established by the Aluminium Association. This system provides valuable information about the composition and characteristics of different aluminium alloys. The first digit in the numbering system signifies the major alloying elements, while the subsequent digits indicate specific variations within each alloy. Common alloying elements used in aluminium grades include copper, manganese, silicon, magnesium, and zinc. These alloying elements impart specific properties to the aluminium, making it suitable for various applications. Based on their properties and manufacturing processes, aluminium grades can be classified into two main categories: wrought alloys, which can be shaped into different forms, and cast alloys, which are melted and cast into specific shapes.
Commonly Used Aluminium Grades and Their Properties
- 1000 Series: These grades are pure aluminium with a minimum aluminium content of 99%. They are highly ductile and offer excellent corrosion resistance. 1xxx series alloys, such as 1050 and 1100, are often used in electrical applications, conductive foils, and general-purpose fabrication.
- 3000 Series: These grades incorporate manganese as the major alloying element. They are non-heat treatable and exhibit moderate strength and good formability. 3xxx series alloys, such as 3003 and 3004, are commonly used in cooking utensils, heat exchangers, and architectural applications.
- 5000 Series: These grades contain magnesium as the primary alloying element. They offer good corrosion resistance, weldability, and moderate strength. 5xxx series alloys, such as 5052 and 5083, are widely utilized in marine applications, automotive parts, and storage tanks.
- 6000 Series: These grades incorporate silicon and magnesium as the major alloying elements. They offer excellent extrudability and are often used for structural applications. 6xxx series alloys, such as 6061 and 6063, are commonly employed in construction, furniture, and automotive components.
- 7000 Series: These grades are known for their high strength and excellent machinability. They typically contain zinc as the primary alloying element. 7xxx series alloys, such as 7075, are widely used in aerospace components, bicycle frames, and high-performance applications.
- 8000 Series: These grades are often used for specialized applications. They include alloys like 8011, which is commonly used in packaging foils, and 8006, which is utilized in the production of beverage cans.

Advantages of Aluminium for Metal Fabrication
Lightweight and High Strength-to-Weight Ratio
One of the primary advantages of aluminium in metal fabrication is its remarkable lightweight nature coupled with an impressive strength-to-weight ratio. Weighing only about one-third as much as stainless steel, aluminium offers an excellent balance between strength and weight. This characteristic makes it an ideal choice for industries where weight reduction is crucial, such as in the manufacturing of transportation vehicles. For instance, in the aerospace industry, aluminium is extensively used to construct aircraft components, including wings, fuselages, and engine parts. Commercial airplanes like the Boeing 787 Dreamliner utilize aluminium extensively to reduce weight, enhance fuel efficiency, and increase the overall range.
Ease of Workability and Corrosion Resistance
Aluminium’s exceptional workability is another advantageous feature in metal fabrication projects. Being a soft metal, aluminium is easily shaped, formed, and manipulated, allowing for intricate designs and complex structures. This versatility is highly valued in manufacturing industries, where aluminium is employed for the production of various products. For example, in the automotive manufacturing sector, aluminium is utilized to fabricate engine blocks, cylinder heads, and suspension components. The use of aluminium in these parts helps reduce vehicle weight, improve fuel efficiency, and enhance overall performance.
Non-Magnetic Properties for Electrical Applications
Aluminium’s non-magnetic properties make it a favoured material for electrical applications that involve magnet-sensitive system components. Unlike ferrous metals, aluminium does not interfere with magnetic fields, making it ideal for industries such as electronics manufacturing. A prominent example is the production of electrical enclosures and housing for electronic devices. Aluminium enclosures provide electromagnetic shielding and protect sensitive components from interference, ensuring optimal performance and reliability.
Aluminium Fabrication Techniques
Aluminium, like other commonly used metals, can undergo various fabrication methods to shape and transform it into desired products. However, when working with this versatile material, certain techniques yield superior results. In this article, we will explore valuable tips for fabricating aluminium using some of the more prevalent and effective methods. While we have previously discussed fundamental metal fabrication types in a separate article, this time we specifically focus on aluminium fabrication and the techniques that bring out its full potential.
- Extrusion: Among the available methods, extrusion imposes minimal stress on aluminium. This process involves forcing aluminium through or around a die, which can either be open or closed. By doing so, the metal conforms to the die’s size and shape. Extrusions can be performed either in a hot state, where the metal is heated, or in a cold state, where the metal remains at room temperature.
- Drawing: Drawing entails pulling metal through a tapered die to stretch it. Deep drawing specifically refers to achieving a resulting product with a depth equal to or greater than its width. Aluminium is frequently drawn into wire and utilized for products like cans due to its remarkable ductility. Notably, this method is particularly suitable for the 3003, 5005, and 5052 aluminium alloys.
- Forming: Aluminium’s inherent flexibility and softness make it well-suited for forming processes such as bending, stamping, and rolling. While the 3003 alloy excels in this regard, the 5052 and 6061 varieties also exhibit favourable characteristics. Additionally, most alloys belonging to the 1000, 2000, 4000, and 5000, families can be effectively formed. Forming involves applying pressure to part or all of a sheet or plate to shape it according to the desired end product.
- Castings: Castings are created by pouring liquid metal into a mould or die. Optimal results are achieved using 4000 and 5000 alloys, renowned for their strength and wear resistance.
- Forging: Forging is the process of shaping metal through beating or compression. This method is particularly advantageous for applications requiring exceptional durability, especially in stress-bearing parts.
- Machining: Machining encompasses turning and milling processes, best accomplished using aluminium grades 6061 and 7075. Machining involves a subtractive cutting technique that sculpts by removing metal. With aluminium, it is crucial to employ specialized tools and lubricants due to the metal’s unique thermal properties, which can pose challenges when using conventional equipment.
- Waterjet Cutting: Waterjet cutting involves the high-pressure spraying of water with abrasives and does not involve the use of heat. This method avoids altering aluminium’s properties as laser cutting might. However, alternative methods such as laser cutting, or plasma cutting can also be employed to cut aluminium.
- Welding: MIG and TIG welding techniques, which involve melting a metal thread to bind two aluminium pieces together, are most effective when working with 1000 and 3000-6000 aluminium alloys. Friction welding can also be advantageous when attaching aluminium to other metals.
- Adhesive Bonding: Adhesive bonding is a commonly utilized method for assembling aluminium, as certain adhesives adhere well to the outer layer of aluminium oxide.
Conclusion
Aluminium fabrication offers numerous advantages and plays a significant role in various industries. Its lightweight nature, workability, corrosion resistance, and versatility make it a preferred choice for diverse fabrication projects. The availability of different grades of aluminium further enhances its applications in fabrication. Each grade has its specific composition and properties, designed to meet various requirements. The use of aluminium in construction allows for the construction of towering skyscrapers and intricate facades, while its presence in the manufacturing sector enables the production of consumer electronics and precision parts. In the automotive and aerospace industries, aluminium’s lightweight design enhances fuel efficiency and performance. Through a range of fabrication techniques, such as extrusion, casting, forging, and machining, aluminium can be shaped and transformed to meet specific requirements, further expanding its applications across industries.