Galvanized steel is one of the most commonly used materials in various industries, from construction to automotive manufacturing. It is known for its exceptional strength, durability, and corrosion resistance. The process of hot dip galvanizing, which involves coating steel with a layer of zinc, provides these desirable qualities. In this article, we will discuss the basics of hot dip galvanizing, with particular focus on its advantages and common applications.
What is Hot Dip Galvanizing?
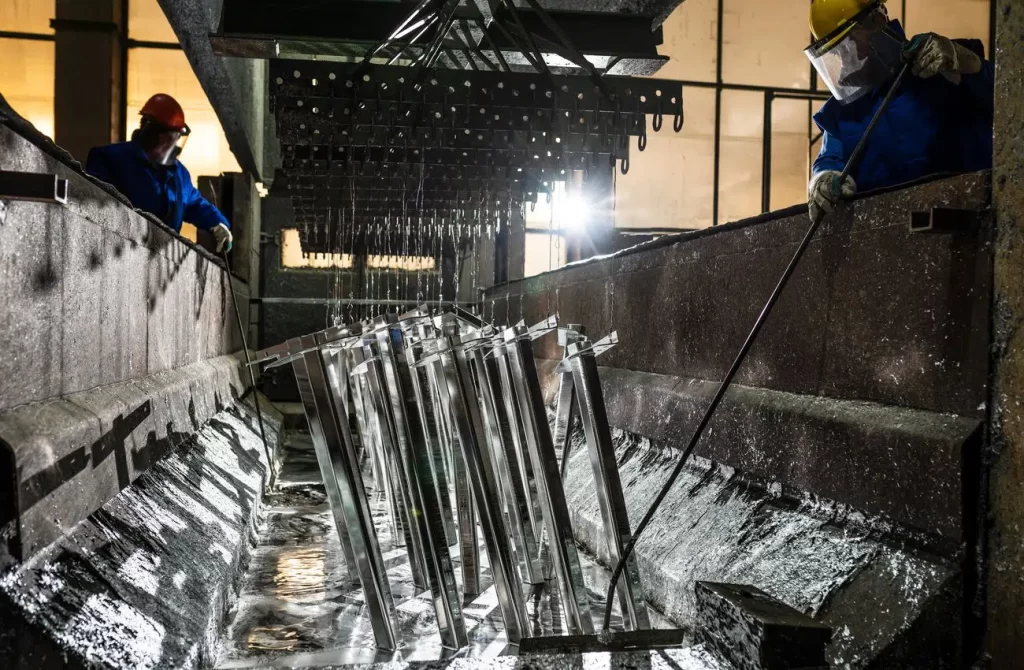
Hot-dip galvanization is like giving your iron or steel objects a hot and bubbly zinc bath! First, the metal object is dipped into a heated zinc bath, which is around 450°C. When it comes out of the molten bath, the zinc coating on the metal reacts with oxygen in the air to create a layer of zinc oxide (ZnO).
But that’s not the end of the story! The zinc oxide layer then reacts with carbon dioxide, creating a protective layer called zinc carbonate (ZnCO3). This layer looks like a dull grayish film, but it is a tough and stable layer that firmly covers the surface of the iron or steel. In hot-dip galvanization, the zinc bonds with the metal and becomes a part of the protected surface. Although hot-dip galvanization might seem like a simple process, it actually consists of several steps that are all necessary for it to be performed correctly.
The Process of Hot Dip Galvanizing
Surface Preparation
When the fabricated steel arrives at the galvanizing facility, it is hung by wire or placed in a racking system which can be lifted and moved through the process by overhead cranes. The steel then goes through a series of three cleaning steps: degreasing, pickling, and fluxing.
Degreasing
Degreasing removes dirt, oil, and organic residues from the surface of the steel. The steel is first immersed in an alkaline solution to remove the bulk of the oils and greases, followed by a rinse in a water tank. A second degreasing process involves immersing the steel in an acid solution to remove any remaining grease, oils, or rust.
Pickling
The next step is pickling, where the steel is immersed in an acidic solution to remove mill scale and iron oxide from the surface of the steel. Pickling is necessary because zinc will not react with unclean steel.
Fluxing
The final surface preparation step, fluxing, will remove any remaining oxides and coat the steel with a protective layer to prevent any further oxide formation prior to galvanizing. The flux solution contains a mixture of ammonium chloride, zinc chloride, and potassium chloride.
Galvanizing
After surface preparation, the steel is dipped in the molten bath (450°C) of at least 98% zinc. The steel is lowered into the kettle at an angle that allows air to escape from tubular shapes or other pockets, and the zinc to flow into, over, and through the entire piece. While immersed in the kettle, the iron in the steel metallurgically reacts with the zinc to form a series of zinc-iron intermetallic layers and an outer layer of pure zinc.
Inspection
The final step is an inspection of the coating. A very accurate determination of the quality of the coating can be achieved by a visual inspection, as zinc does not react with unclean steel, which would leave an uncoated area on the part. Additionally, a magnetic thickness gauge can be used to verify the coating thickness complies with specification requirements.
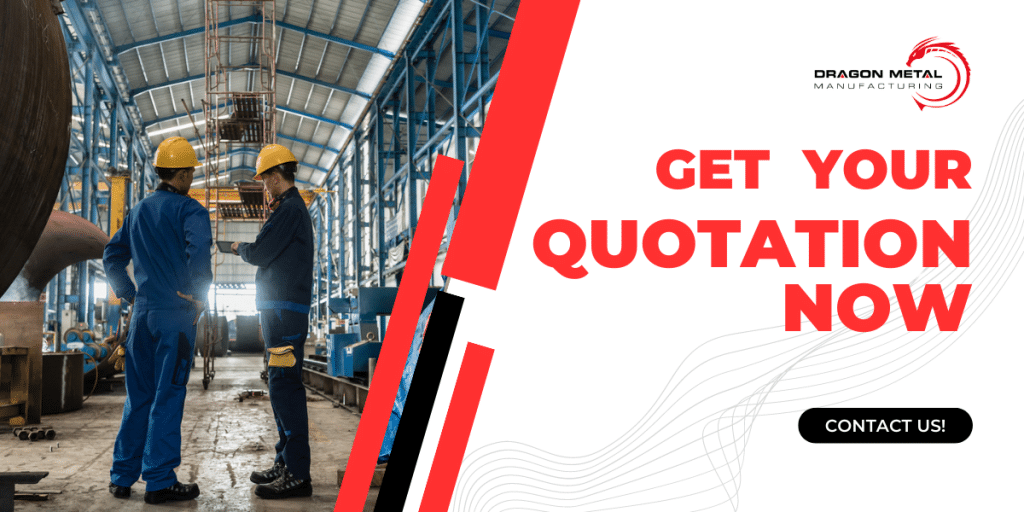
Advantages of Galvanized Steel
Galvanized steel offers several advantages over other coatings and materials. Here are the 10 advantages based on Galvanizers Association of Australia:
1. Low First Cost
One of the most significant advantages of galvanizing steel is its low first cost. Galvanizing is cheaper than many other commonly specified protective coatings for steel. While labour-intensive coatings like painting have become more expensive, the cost of factory operations like galvanizing has remained relatively stable. As a result, galvanizing is a cost-effective way to protect steel structures and equipment.
2. Less Maintenance/Lowest Long-Term Cost
Even in cases where the initial cost of galvanizing is higher than alternative coatings, galvanizing is almost always the cheapest option in the long term. Galvanized coatings last longer and require less maintenance than other coatings, which can save money over time. Additionally, maintenance can cause problems and add to costs, especially in remote areas or when production is disrupted.
3. Long Life
Galvanized coatings have an incredibly long-life expectancy. In most rural environments, the life expectancy of galvanized coatings on typical structural members is far in excess of 50 years. Even in severe urban and coastal exposure, galvanized coatings can last for 20 to 25 years or more.
4. Reliability
Galvanizing is carried out to strict standards like Australian/New Zealand Standard 4680, and standard minimum coating thicknesses are applied. Coating life and performance are reliable and predictable, providing peace of mind to those who choose to use galvanizing for their steel structures and equipment.
5. Tough Coating
The metallurgical structure of a galvanized coating provides outstanding resistance to mechanical damage during transport, erection, and service. This toughness makes galvanizing an excellent choice for steel structures and equipment that will face harsh conditions.
6. Automatic Protection for Damaged Areas
Galvanized coatings corrode preferentially to steel, providing cathodic or sacrificial protection to small areas of steel exposed through damage. This means that small, damaged areas do not require touch-up, unlike organic coatings that need to be repaired when damaged.
7. Complete Protection
Every part of a galvanized article is protected, including recesses, sharp corners, and inaccessible areas. No coating applied to a structure or fabrication after completion can provide the same level of protection.
8. Ease of Inspection
Galvanized coatings can be assessed readily by eye, and simple non-destructive thickness testing methods can be used. If coatings appear to be sound and continuous, they are likely to be so, making inspection easy and straightforward.
9. Faster Erection Time
As galvanized steel members are received, they are ready for use. No time is lost on-site in surface preparation, painting, and inspection. When assembly of the structure is complete, it is immediately ready for use or for the next construction stage, which can speed up construction time and improve project timelines.
10. Full Protective Coating in Minutes The galvanizing process is not dependent on weather conditions, and a full protective coating can be applied in minutes. This speed and efficiency make galvanizing an attractive choice for those looking to protect their steel structures and equipment.
Common Applications of Galvanized Steel
Galvanized steel is an immensely versatile material that has various uses across numerous industries. One of the most prevalent applications of this material is in construction, where it is frequently used for roofing, siding, and framing materials. Its exceptional strength and resilience make it ideal for such applications, as it can endure the severe elements and harsh weather conditions that are often present in many regions.
Aside from construction, galvanized steel is also employed in the production of metal fittings like nuts, bolts, and screws, which have a wide range of applications in industries ranging from automobile manufacturing to industrial machinery and equipment. The robustness and corrosion resistance of galvanized steel make it an excellent material for these sorts of applications, as it can withstand exposure to harsh chemicals and other corrosive substances.
Another common application of galvanized steel is in the production of household and kitchen appliances. Due to its superb resistance to corrosion and rust, galvanized steel is frequently used for the inner components of appliances such as refrigerators and dishwashers. It is also commonly used for the outer casings of appliances, imparting a modern and sleek appearance that is both easy to clean and maintain.
Lastly, the automotive industry is another sector where galvanized steel is widely utilized. It is employed for numerous parts, including body panels, exhaust systems, and suspension components. The material’s excellent corrosion resistance and durability make it highly suitable for these applications, as it can endure the severe road conditions and exposure to salt and other corrosive materials.
All in all, galvanized steel is an incredibly versatile material that has a broad range of uses across various industries. Its superior strength, durability, and corrosion resistance make it an excellent material for construction, manufacturing, and automotive applications, as well as for household and kitchen appliances.
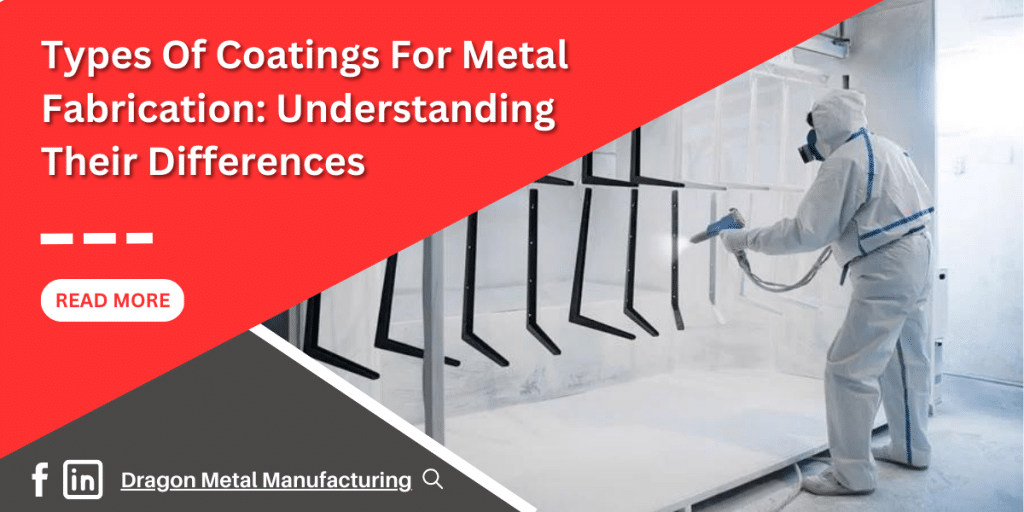
Comparison between Galvanization and Powder Coating
One of the most fundamental differences between hot dip galvanizing and powder coating lies in how they protect the surface of the workpiece. Galvanization works by offering up sacrificial protection, meaning that the coating absorbs corrosive substances before they can attack the metal object. Powder coating, on the other hand, works by creating a protective barrier that prevents destructive materials from infiltrating and harming the surface.
The effectiveness of hot-dip galvanization in preventing corrosion makes it an excellent choice for safeguarding outdoor objects that are exposed to the elements, such as iron and steel gates, fences, and guardrails. Powder coating, by comparison, offers greater versatility when it comes to decorative purposes, offering a wide range of colors and textures that are more suitable for indoor products.
Hot Dip Galvanizing Standards and Specifications
Hot Dip Galvanizing Standards and Specifications in Australia are critical to ensure the quality and durability of galvanized steel products. The Australian standard for hot-dip galvanizing is AS/NZS 4680, which outlines the minimum requirements for the coating thickness, appearance, and adhesion of the galvanized layer. This standard also sets out the preparation and inspection procedures for galvanized coatings, including the necessary pre-treatment and post-treatment processes.
In addition to the AS/NZS 4680 standard, other relevant Australian standards for hot dip galvanizing include AS 1214, which outlines the sampling procedures for determining the thickness of the zinc coating, and AS 2312.2, which covers the design and durability of galvanized steel products. Compliance with these standards is crucial for ensuring that galvanized steel products are fit for purpose and can withstand the harsh Australian environment. At the same time, it is important to note that adherence to these standards does not necessarily guarantee the longevity of the coating, as factors such as the quality of the steel substrate, exposure conditions, and maintenance practices can also affect the performance of the galvanized layer.
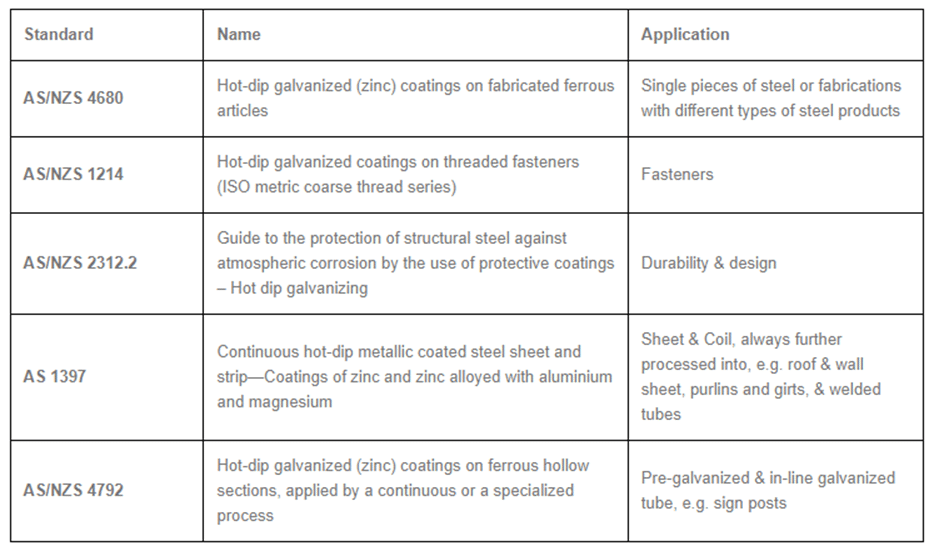
Conclusion
Hot dip galvanizing is an effective and reliable coating process for steel, providing numerous benefits in terms of corrosion resistance, durability, and cost-effectiveness. Despite its limitations, galvanized steel remains a popular choice for a wide range of applications, from construction and infrastructure to automotive and industrial manufacturing. By understanding the basics of hot dip galvanizing and working with experienced and knowledgeable galvanizing professionals, businesses and individuals can ensure the highest quality and performance of their galvanized steel products.
Frequently Asked Questions
What is the difference between galvanized steel and stainless steel?
Galvanized steel is coated with a layer of zinc to provide protection against corrosion and rust, while stainless steel contains chromium to resist rust and staining.
Can galvanized steel be painted over?
Yes, galvanized steel can be painted over, although it is important to properly prepare the surface before painting to ensure adhesion.
How long does galvanized steel last?
Galvanized steel can last for many years, with a typical lifespan of 50 years or more in outdoor environments.
Is galvanized steel magnetic?
Galvanized steel is magnetic, as it is made from a ferrous material (steel) coated with a layer of zinc.
Can galvanized steel be welded?
Yes, galvanized steel can be welded, although it is important to take proper precautions to avoid damaging the zinc coating during the welding process.