Welcome to our blog post on micromachining – a process that has been revolutionizing the way small and precise components are manufactured for several years now. As an engineer, you understand the critical role that micromachining plays in industries such as aerospace, medical, and electronics. In this post, we will explore what micromachining is, the various techniques used, and its significance in precision manufacturing. Join us as we delve into the world of micromachining and discover how this technology is changing the way we produce miniature components.
What is Micromachining?
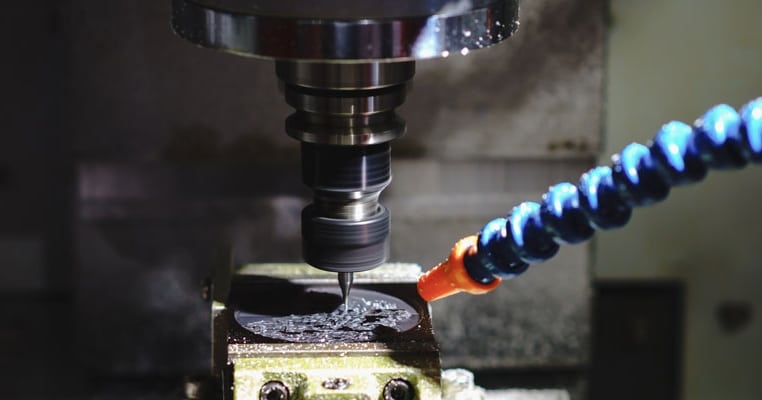
Micromachining is a precise form of manufacturing that creates small parts with high accuracy, typically on the sub-millimetre scale. This multi-step process utilizes specialized tools and techniques to produce components that are critical to various industries, from aerospace to medical devices. But micromachining isn’t just about making small parts – it’s also used to create microstructures and microfeatures. Microstructures are tiny features that can be added to surfaces to enhance their functionality, while microfeatures refer to small geometric shapes and designs used in a range of applications.
Take a close look at the surface of a tiny electronic device, like a smartwatch or a hearing aid, and you’ll marvel at the intricate patterns etched into its surface. These microstructures and microfeatures are created through the fascinating world of micromachining. With its ability to create small parts and intricate designs with high accuracy, micromachining is changing the way we approach precision manufacturing. From aerospace to medical devices, this technology plays a vital role in producing the tiny components that make our world go round.
What are the Micromachining Processes?
The two main categories of micromachining are bulk micromachining and surface micromachining. Bulk micromachining involves the removal of material from a substrate to create a desired shape or structure, while surface micromachining involves the deposition and patterning of thin films to create a desired shape or structure. However, it’s worth noting that some processes, such as DRIE (Deep Reactive Ion Etching) or LIGA (Lithography, Galvano forming, and Moulding), do not fit neatly into these categories. Instead, they involve more specialized techniques that are tailored to specific applications.
Bulk Micromachining
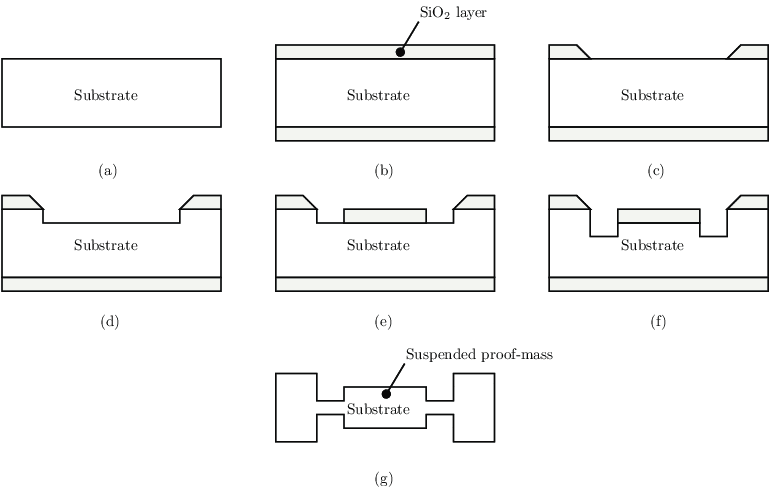
Bulk micromachining is a technique used for creating tiny mechanical or electrical components. Unlike surface micromachining, which builds a component layer by layer, bulk micromachining starts with a solid piece and removes material until the desired shape is achieved. Typically, silicon wafers are used for this process, although plastic or ceramic may also be used occasionally.
The most commonly used methods for bulk micromachining are selective masking and wet chemical solvents, although dry etching using a plasma or laser system is becoming increasingly popular. Although dry etching is more expensive than wet etching, it is also considered more precise.
Bulk micromachining is commonly used in creating microelectromechanical systems (MEMS) devices. The process involves removing material from the entire volume of a substrate to create microstructures or features. The etchant used selectively removes material while leaving the desired microstructure or feature intact, resulting in either a three-dimensional shape or a two-dimensional pattern.
One advantage of bulk micromachining is its ability to create complex three-dimensional structures with high aspect ratios, making it an invaluable technique for making microchannels, microvalves, and micromirrors. These structures have a wide range of applications, from medical devices to sensors and optical devices.
However, achieving high precision and accuracy with bulk micromachining can be challenging, particularly for structures with complex geometries. Additionally, the etching process can introduce defects or residual stresses in the material, which can affect the mechanical and electrical properties of the resulting structure. Therefore, careful optimization and control are necessary to achieve the desired results. In summary, bulk micromachining is a fascinating technique that has revolutionized the creation of tiny components. While it has some limitations, it remains an essential process for the production of MEMS devices and other microstructures. The ongoing development of this technique is sure to bring further advances in the field of micromachining.
Surface Micromachining
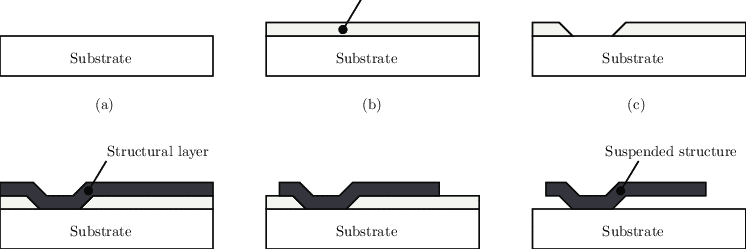
Surface micromachining is a manufacturing process that enables the creation of integrated circuits and sensors with exceptional precision. It involves the deposition of thin films of various materials on a substrate and the selective removal of these layers to create the desired circuit patterns. The technique allows for the creation of nearly 100 finely applied layers of circuit patterns on a single chip, which is a significant improvement over the standard processes that can only produce five or six layers. This ability to incorporate multiple layers of circuitry allows for the integration of more functions and electronics into each chip, making it ideal for use in motion sensors, accelerometers for deploying airbags during vehicle crashes, and gyroscopes for navigation systems.
This process typically involves the use of materials such as silicon nitride, silicon dioxide, and polysilicon. The process can involve a variety of techniques, including chemical vapor deposition, photolithography, and plasma etching. Both wet and dry etching processes are used to achieve the desired circuit patterns, offering high precision and allowing for the creation of complex structures. However, the complex layer-by-layer process can be time-consuming and expensive, and the resulting structures may be susceptible to residual stresses that can affect their mechanical and electrical properties.
One of the advantages of surface micromachining is its ability to produce intricate, high-precision structures with very smooth surfaces. This technique is often used for the production of microelectromechanical systems (MEMS) devices and micro-optical components. In contrast to bulk micromachining, surface micromachining allows for the creation of features with relatively high aspect ratios, though typically not as high as those achievable with bulk micromachining.
Despite its limitations, surface micromachining is a valuable technique for creating complex microstructures and components, particularly those with smooth surfaces and high precision. In comparison to bulk micromachining, surface micromachining may be more suitable for structures with less extreme aspect ratios, and it may offer greater precision in some cases. Ultimately, the choice between bulk and surface micromachining will depend on the specific requirements of the application at hand.
Why is Micromachining Essential?
Micromachining plays a crucial role in a range of industries, including aerospace, medical, and electronics. In aerospace, micromachining is instrumental in the production of key components like turbine blades, fuel injectors, and hydraulic system parts. In the medical field, micromachining enables the creation of tiny implants, surgical tools, and other medical devices. In electronics, micromachining allows for the development of microelectronics and other electronic components.
The precision and accuracy offered by micromachining are vital to modern manufacturing, enabling the creation of high-quality components that meet stringent specifications. As technology continues to advance, the applications of micromachining are expanding, making it an exciting and rapidly evolving field with tremendous potential for innovation. As such, micromachining is a vital and indispensable aspect of modern manufacturing.
Conclusion
In conclusion, micromachining is a critical process for precision manufacturing in a variety of industries, including aerospace, medical, and electronics. If you have an inquiry that involves micromachining or other specialized manufacturing processes, Dragon Metal Manufacturing may be able to help find a solution. Our network of suppliers includes experts in many fields, and we are dedicated to providing our clients with the highest quality components and services. Contact us today to discuss your manufacturing needs and learn how we can help you find the best solutions.