Have you ever wondered how the products you use every day are made so quickly and efficiently? Well, automation in manufacturing is the answer! This basically means using technology to automate different processes in the production of goods, from simple tasks like sorting and packaging to complex processes like assembly and quality control. The ultimate goal of automation is to improve efficiency, reduce costs, and increase productivity, which is why the manufacturing industry has seen significant growth in automation over the past few decades.
In fact, according to the International Federation of Robotics, there were approximately 2.7 million industrial robots operating in factories worldwide in 2019 – that’s a 12% increase from the previous year! This growth in automation has allowed manufacturers to shift their focus to designing, operating, directing, installing, and troubleshooting automated systems, robots, software, machine algorithms, and equipment, which has in turn increased productivity and output.
If manufacturers want to stay competitive in modern manufacturing scenarios, they must consider industrial automation to maintain their competitiveness. In this article, we’ll have a look at the three main manufacturing automation systems and dive into each type exploring some of their benefits.
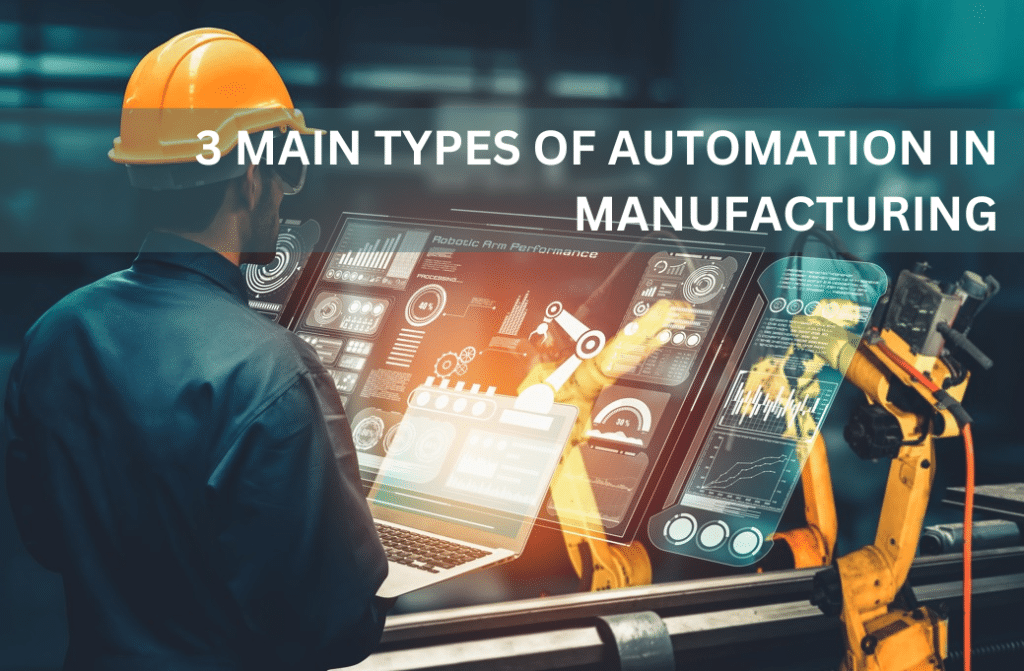
1) Fixed Automation in Manufacturing
Fixed automation is a manufacturing system which uses a predetermined sequence of operations, and the equipment and machinery used in the production process are designed to perform a specific task (or set of tasks) repeatedly in the same way without variation. This system is typically designed for mass production of a single product or of a small range of products, and it is very difficult to adapt it to new production requirements or changes.
Fixed Automation Examples
- Assembly lines. Assembly lines are a good example of fixed automation. An assembly line is generally made up of a series of fixed stations and automated equipment that perform the same task repeatedly.
- Conveyors. Conveyors are even more a clear example of automation. They are used to move products from one station to another and they are designed to perform the same task repeatedly.
- Robotic Welding. Robotic welders are designed to perform the same welding task repeatedly, without significant customization or reprogramming between jobs. Robotic welders generally use pre-programmed welding paths and parameters to ensure consistent and efficient operation.
2) Programmable Automation in Manufacturing
Programmable automation, on the other hand, refers to a type of manufacturing system that uses computer-controlled equipment and machinery to perform a variety of tasks. Unlike fixed automation, the sequence of operations and equipment used in programmable automation can be easily changed or reprogrammed to accommodate changes in product design or production requirements.
Programmable Automation Examples
- Computer Numerical Control (CNC) machines. CNC machines are programmable automation systems that are used for machining tasks like milling, turning, and tapping. They are capable of accurately producing complex designs, but they are typically designed to perform a specific set of tasks and require significant reprogramming to adapt to new production requirements.
- Programmable logic controllers (PLCs). PLCs are used to automate manufacturing processes, such as assembly lines and packaging systems. They can perform a wide range of control functions but are not easily adaptable to new production requirements without reprogramming.
- Industrial robots. Industrial Robots are used for a wide range of manufacturing tasks, including welding, painting, and assembly. While robots can be programmed to perform multiple tasks, they are typically designed for a specific set of applications.
3) Flexible Automation in Manufacturing
FFlexible automation is a type of manufacturing system that is designed to be versatile and adaptable. In fact, it can handle a wide variety of production tasks simultaneously. Unlike fixed automation, which is designed to perform a specific task repeatedly, or programmable automation, which can handle a variety of tasks but requires significant reprogramming to adapt to new tasks, flexible automation is capable of handling multiple tasks simultaneously without the need for major reprogramming.
Flexible Automation Examples
- Robotic Assembly Systems with Vision System. These systems are designed to perform a variety of tasks, from inserting screws and attaching components to tightening bolts. When equipped with vision systems, these robots can recognise and adjust to variations in product size, shape and orientation without needing to be reprogrammed.
- Automated Material Handling Systems with smart sensors. Like for enhanced robotic assembly systems, when equipped with smart sensors, automated material handling systems can detect changes in product size and weight and carry out a variety of tasks without reprogramming.
- AGVs (Automated guided vehicles). These are used to transport materials between different manufacturing facilities. They can be programmed to follow a specific route and can carry out a wide range of tasks, like loading and unloading goods.
Conclusion
When it comes to automation in manufacturing, there are three main types to consider: fixed, flexible and programmable. Fixed automation is best suited for specific and repetitive tasks, especially production focused. Flexible and programmable automation appear to be quite similar to one another. However, while both flexible and programmable automation involve the use of automation technology, they differ in their focus and approach. Flexible automation is focused on adaptability and versatility, while programmable automation is focused on precision and control.