Welding is a vital manufacturing process that bonds metal pieces by heating them until they melt and then cool, fusing them together. This technique is crucial in various industries, from building bridges to making cars. Welding techniques have progressed over time to enhance the quality and efficiency of the process. Manufacturers need to keep pace with the latest welding techniques to produce top-notch products efficiently.
This article will discuss the welding techniques’ evolution and their potential to enhance manufacturing. By exploring the latest welding technology, we’ll demonstrate how manufacturers can upgrade their products’ quality and efficiency, leading to increased success and profits.
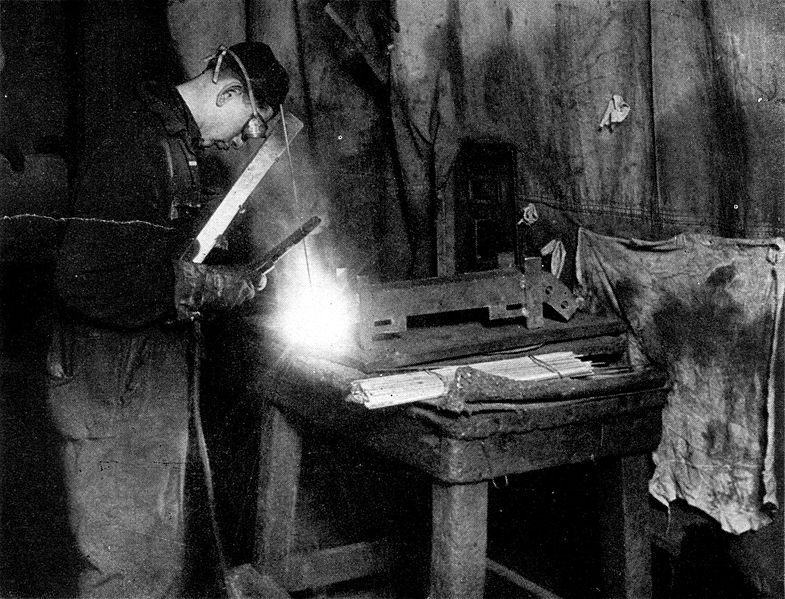
History of Welding Techniques
Welding has been around for centuries. Bronze Age gold boxes were assembled using brazing. However, welding became a widely used industrial technique in the 19th century.
In the 1800s, the introduction of the electric arc was created, and in 1881, Auguste de Meritens created the first electric arc welding process. Modern welding techniques we know today weren’t developed until the 1930s.
Stick welding, the oldest welding technique, uses a welding electrode to create an electric arc.
TIG welding, known for its precision, uses a non-consumable tungsten electrode and a shielding gas.
MIG welding uses a consumable wire electrode and a shielding gas.
FCAW uses a hollow wire filled with flux, while SAW uses a continuously fed wire electrode submerged under a layer of flux.
Gas welding uses a flame from the combustion of a fuel gas and oxygen.
These traditional welding techniques have various applications and advantages.
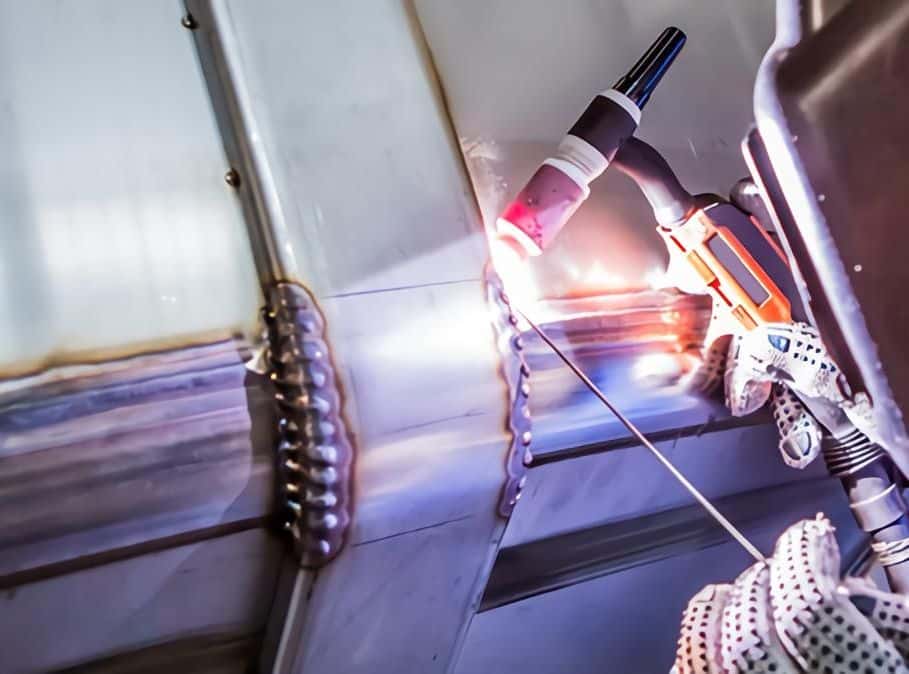
Advancements in Welding Techniques
Over the years, welding process improved efficiency, quality, and safety with the several advancement of welding techniques Here are some modern welding techniques:
- Laser Welding: Uses a focused laser beam for precision and speed. Ideal for thin and delicate materials and produces a clean and aesthetic weld.
- Electron Beam Welding: Uses high-speed electrons to join parts with high speed, narrow heat-affected zone, and high penetration depth. Often used in aerospace and medical industries.
- Friction Stir Welding: Uses a non-consumable tool to soften metal and create low distortion, low porosity, and high joint strength. Often used in automotive and aerospace industries.
- Plasma Arc Welding: Uses plasma arc for precision, low heat input, and low distortion.
The benefits and drawbacks of different welding techniques vary depending on the application and materials used. Laser welding is efficient and precise for thin sheets, while friction stir welding suits thicker and larger components. The choice of technique depends on specific manufacturing requirements, such as material type, thickness, production volume, and quality standards.
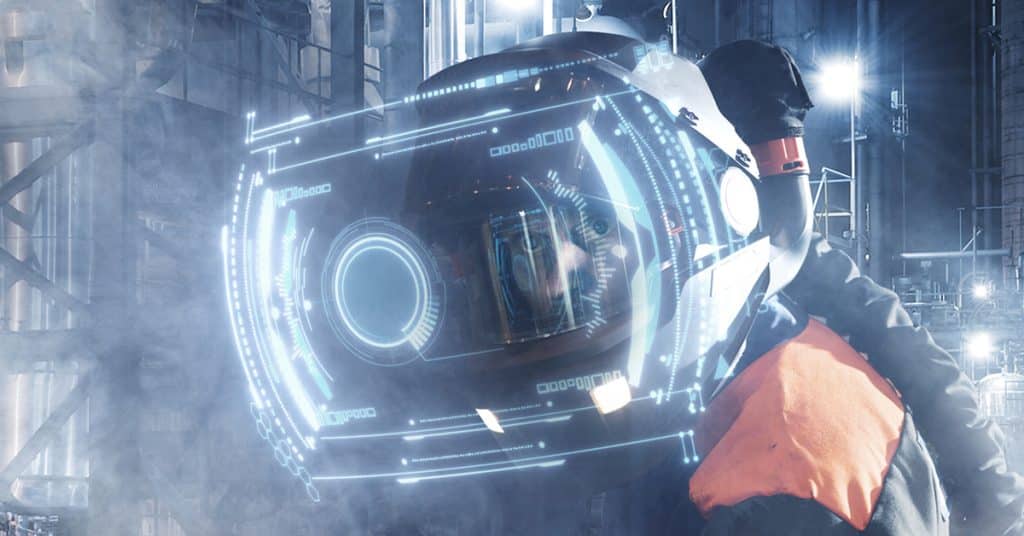
Future of Welding
The welding industry is constantly evolving, and there are several trends and advancements to watch for:
Automation: Automation is becoming increasingly popular in welding, with robots being used to increase speed and accuracy.
Augmented Reality: Augmented reality technology is being used to help welders see their work in real-time, making it easier to spot potential issues before they become major problems.
3D printing: 3D printing is being used to create complex welding structures, which can reduce the need for manual welding.
Understanding the future of welding techniques is important for both professionals and enthusiasts in the field. With advancements in technology, the future of welding looks promising, with automation, augmented reality, 3D printing, and laser welding becoming increasingly popular. By keeping up with the latest trends and advancements, welders can improve their skills and continue to excel in their field.
Conclusion
Traditional welding methods like stick welding, TIG welding, MIG welding, FCAW, SAW, and gas welding have their uses. However, modern techniques such as laser welding, electron beam welding, friction stir welding, and plasma arc welding offer advantages such as high precision, speed, low distortion, and strong joints. To stay competitive, manufacturers must keep up with the latest welding techniques. In addition, trends such as automation, augmented reality, and 3D printing are likely to shape the future of welding. For any inquiries about welding or offshore manufacturing, don’t hesitate to contact Dragon Metal Manufacturing.