For many Australian manufacturers, working in collaboration with Offshore Manufacturing factories across Asia is a necessity. It enables them to optimise their production cycle and remain competitive.
Many companies still prefer manufacturing everything in-house or, in any case, using only local suppliers. Of course this is great for the Australian economy and it is admirable. However, sometimes this means incurring very high shipping costs within Australia and it forces companies to increase their prices, thus becoming less competitive.
In the past China was famous for its cheap and low-quality products, but this is no longer the case. Like Japan and Taiwan before it, China has completely transformed and is now a leading player in the High-tech industry.
Below are 6 ways in which Offshore manufacturing could possibly help reduce production costs:
1. Cheaper Labour Costs:
- Although Labour Costs are increasing in many Asian countries, and in particular in China, it is still much more competitive than in countries like Australia, New Zealand and the US.
- As the labour costs gradually increase, there is also greater deployment of more sophisticated technology, aimed at increasing efficiency, and which in turn results in further cost savings.
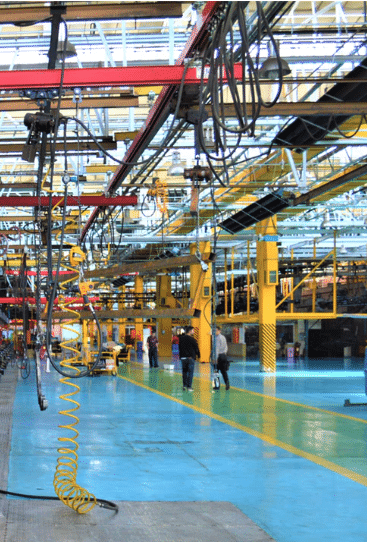
2. Focus on added value services:
- An increasing number of manufacturing companies are outsourcing to add value to their production cycle, keeping only their core competencies in-house. This translates into having resources applied where needed, instead of on inefficient or time-consuming processes.
3. More Competitive Processes:
- There are also certain processes, that are a lot cheaper overseas, be it due to Government regulations or to the greater amount of resources required. All surface treatment, for example,
is considerably cheaper in China, i.e, painting, undercoat, hot dip galvanising.
4. Sourcing, Assembly and Finished Products:
- Very often it is possible to make even greater savings with semi-assembled products and, in some instances, even fully assembled and packaged products. It is not uncommon for manufacturers to have to assemble parts coming from several different suppliers. This can increase costs and also take time away from purchasing managers, who could be working on tasks that add more value.
- Manufacturers are sometimes forced to send parts out several times for additional processes before the parts can be sold. Being able to purchase the finished goods directly from a single supplier has numerous advantages.
5. Shipping Costs:
- Manufacturers in Australia, are well aware of the long shipping time and high costs. When using an offshore manufacturing company it is possible to ship out assembled products to various cities around Australia for very competitive prices and with only an additional 2-3 days on the shipping time. As an example, shipping a 40 foot container from Shanghai to an Australian capital city is similar to the cost of shipping by truck from Melbourne to Sydney.
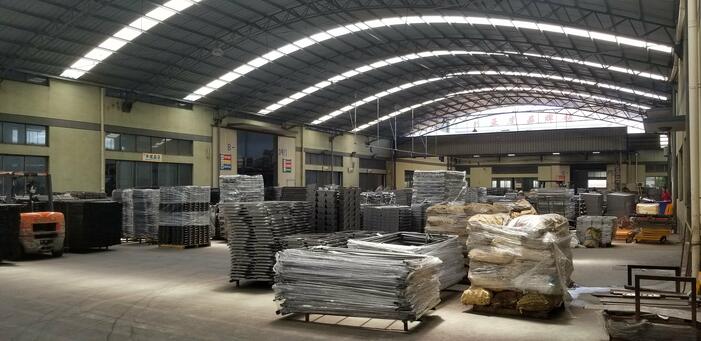
6. Capacity:
- Being able to boost manufacturing capacity with an offshore manufacturing partner, can help meet an increase in product demand, and make it possible to accept orders that would not have otherwise been possible to manufacture in-house.
It is possible to go directly to manufacturers in China but this is fraught with danger, both with substandard products being shipped and unforeseen costs applying. With a sourcing partner like Dragon Metal Manufacturing, quality is guaranteed and all costs are transparent and known prior to ordering.
is a test.